Аммиак как топливо для судов
Обновлено: 26.04.2024
Морская индустрия в поисках углеродно-нейтрального горючего
«Кто владеет нефтью, тот правит миром» ,— эта знаменитая сентенция принадлежит не политику или нефтяному магнату, ее в самом начале XX века высказал адмирал сэр Джон Фишер, знаменитый Первый Морской лорд и реформатор Королевского флота, один из создателей того, что сегодня мы называем геополитикой. Самая известная реформа Фишера — перевод британского флота с угля на жидкое нефтяной топливо. Вслед за военным последовал и торговый флот. Использование передового для того времени энергоносителя обеспечило как технологическое лидерство в кораблестроении, так и геополитическое лидерство Британской империи на морских коммуникациях вплоть до Второй мировой войны. Именно по настоянию Фишера правительство Великобритании инвестировало в покупку акций Англо-Персидской нефтяной компании, известной сегодня как BP.
Несмотря на то, что сегодня, в условиях кризиса нефтяного перепроизводства, это высказывание, очевидно, требует кардинального пересмотра, его исходное основание остается верным и актуальным. Это основание состоит в том огромном значении, которое морская торговля и морские коммуникации имеют для мировой экономики и политики — не меньшее, но даже большее, чем в начале XX века. По данным Конференции ООН по торговле и развитию (UNCTAD), на судовые перевозки в 2019 году пришлось 80% грузооборота мировой торговли [1].
В начале XX века лидерство на море было связано с переходом от угля к нефти. С каким топливом, способным заменить нефтяное судовое топливо, лидерство будет связано в XXI веке? В эпоху энергетического перехода это топливо должно отвечать, в первую очередь, на вызов декарбонизации. По оценкам Международного совета по чистому транспорта (ICCT), морские перевозки сегодня формируют 3–5% от общемировых выбросов углекислого газа, а к 2050 году, если не обеспечить декарбонизацию водного транспорта, будут ответственны за 17% антропогенной эмиссии парниковых газов [2].
Карта эмиссии парниковых газов морским транспортом по состоянию на 2015 год. Источник: Financial Times
Судовым топливом будущего должен стать аммиак, производимый из «зеленого» водорода. По крайней мере, так считает международный консорциум в составе норвежского нефтяного гиганта Equinor, финской двигателестроительной компании Wärtsilä, немецкого концерна MAN Energy Solutions, корейской судостроительной корпорации Samsung Heavy Industries, малайзийской судоходной компании MISC Berhad и крупнейшего в мире морского классификационного общества — Регистра Ллойда [3]. В 2023 году они намерены пустить в эксплуатацию первое в мире судно на аммиаке — принадлежащий норвежской нефтесервисной компании Eidesvik корабль Viking Energy, обслуживающий оффшорные нефтяные платформы. На специально переоборудованном корабле будет смонтирована система хранения жидкого аммиака, аммиачные топливные элементы, которые разрабатывают MAN и Wärtsilä, и электродвигатели, которые будут питаться от этих топливных элементов.
Амбициозный и рискованный характер проекту придает то, что в настоящее время в мире нет ни одного образа судовой энергетической установки на аммиаке, и сама возможность создания такой установки с достаточно высоким КПД и низким уровнем выбросов NOx вызывает обоснованные сомнения. Впрочем, описанный консорциум — не единственный, ведущий работу в этом направлении: аналогичные задачи решают в Японии концерн IHI совместно с Киотским университетом [4], а также Университет Делавэра в США в рамках финансирования со стороны ARPA-E [5].
Запрос на технологию углеродно-нейтральной и при этом экономичной главной судовой энергетической установки чрезвычайно велик в силу обязательства Международной морской организации (IMO) снизить к 2050 эмиссию парниковых газов морским транспортом как минимум в 2 раза по сравнению с уровнем 2008 года [6]. По оценке Международного морского форма (GMF) и Университетского колледжа Лондона, достижение этой цели создаст крупный рынок и потребует в ближайшие 30 лет инвестиций в размере $1,0–1,4 трлн [7]. Эта оценка основана как раз на сценарии применения аммиака как «зеленого» судового топлива. Альтернативный сценарий, который рассматривает ICCT, — применение на кораблях компримированного или сжиженного водорода, о чем мы уже писали.
Маршруты морской торговли аммиаком и портов, располагающих инфраструктурой по отгрузке (синие точки) и приему (красные точки) аммиака по состоянию на 2017 г. Источник: Royal Society
В обзоре по проблеме аммиака как энергоносителя, подготовленном Лондонским королевским обществом [8], вводятся три типа аммиака, обозначаемые цветами, — по аналогии с водородом в зависимости от технологии производства и величины углеродного следа:
- «Коричневый» аммиак — из природного газа без использования технологий фиксации углекислого газа. Его стоимость без учета платы за эмиссию оценивается в €170–320 за тонну.
- «Голубой» аммиак — из природного газа с применением технологии CCUS. Стоимость без учета платы за эмиссию оценивается в диапазоне €190–360 за тонну в зависимости от того, на всех ли стадиях процесса используется технология CCUS.
- «Зеленый» аммиак — из «зеленого» водорода, произведенного электролизом с использованием электроэнергии от ВИЭ. Стоимость оценивается в широком диапазоне €220–1220 за тонну в зависимости от LCOE производства электроэнергии на основе ВИЭ в том или ином регионе.
Приведенная стоимость аммиака (€ за тонну) и эмиссия парниковых газов при производстве аммиака (тонна на тонну аммиака). Источник: Royal Society
Технология производства «зеленого» аммиака объединяет хорошо отработанные технологии электролиза воды и процесса Габера — Боша, ее TRL достигает 5–9 в зависимости от исполнения. Пилотные установки-демонстраторы производительностью 20–30 кг в день работают в Фукусимском институте возобновляемой энергетики (AIST) в Японии и Лаборатории Резерфорда — Эплтона (RAL) в Великобритании [9].
Принципиальная схема производство “зеленого” аммиака с использование батареи твердо-оксидных электролизных ячеек (SOEC), разрабатываемых в проекте SOC4NH3. Источник: Royal Society
Оригинальную разработку альтернативной технологии получения углеродно-нейтрального аммиака ведет датская компания Haldor Topsøe в кооперации с Орхусским университом, Техническим университетом Дании, датским системным оператором и компаниями Vestas, Equinor и Ørsted в рамках проекта SOC4NH3 [10]. Цель проекта — создание батареи твердо-оксидных электролизных ячеек, способных осуществлять одновременно электролиз воды и сепарацию воздуха с выделением кислорода. Ожидается, что эта технология позволит на 5–10% снизить расход энергии на производство аммиака.
Принципиальная схема производства и применения аммиака в качестве энергоносителя и химического сырья. Источник: Royal Society
Дополнительный стимул проектам, связанным с «зеленым» водородам, в частности, проектам по производству и применению углеродно-нейтрального аммиака должно придать то, что поддержке таких водородных проектов уделяется очень большое внимание в рамках новой, пост-коронавирусной редакции «Европейской зеленой сделки» — пакета мер «Зеленой сделки по восстановлению экономики» [11]. В частности, в сфере водородной энергетики теперь будет использован такой хорошо зарекомендовавший себя механизм косвенного субсидирования, как контракты на разницу цен (CfD). Механизм предполагает заключение контракта между консорциумом, реализующим проект в области производства «зеленого» водорода, и назначенной ЕС банковской структурой, по которому эта структура обязана компенсировать консорциуму потери, возникшие ввиду потенциальной разницы между заявленной в проекте ценой водорода и той ценой, которая установится на момент выхода проекта на рынок. Таким образом, в рамках «Зеленой сделки» за счет CfD, по сути, страхуется маржинальность первой волны водородных проектов, попадающих под действие пакета мер ЕС.
Подготовлено IC ENERGYNET / Автор: Игорь Чаусов
Многие компании видят реальную возможность использования аммиака в качестве топлива в будущем. Как источник энергии аммиак в девять раз мощнее литиево-ионных батарей и почти в два раза энергетически плотнее жидкого водорода, при этом аммиак проще перевозить, чем водород.
Перевод Татьяна Давыдова
Почему об этом говорят?
В наше время «зеленый» аммиак все чаще обсуждают участники рынка аммиака и судоходные компании. Интерес к этому продукту объясняется в том числе предпринимаемыми во всем мире усилиями по снижению выбросов углерода в ближайшие десятилетия. Если при производстве одной тонны обычного аммиака выброс CO2 доходит до двух тонн, то при выпуске «зеленого» аммиака с использованием возобновляемых источников энергии выбросов углерода не будет вовсе.
Мировое производство аммиака сейчас составляет 180 млн т/год. Однако его возможное использование в качестве энергоносителя может привести к увеличению спроса до миллиардов тонн. В настоящее время аммиак считается одним из основных видов топлива в судовых перевозках, использование которого может помочь достижению целевых уровней по выбросам CO2 для судоходства на 2030 г. и 2050 г. Кроме того, аммиак рассматривается как способ хранения возобновляемой энергии для использования позднее, а также как способ транспортировки водорода.
Широкое использование аммиака в этих целях возможно лишь при условии значительного сокращения выбросов CO2 при его производстве. Для этого потребуются огромные инвестиции в развитие новых технологий и увеличение эксплуатационных расходов, если учесть текущую стоимость возобновляемых энергоносителей.
«Зеленый» аммиак как судовое топливо
С начала текущего года введены новые требования IMO 2020, ограничивающие содержание серы в бункерном топливе. Следующий шаг в судоходной отрасли — резкое сокращение выбросов CO2. Пока планируется добиться снижения этих выбросов на 40% к 2030 г. и на 70% — к 2050 г. по сравнению с уровнями 2008 г.
Увеличение эффективности и замена углеводородного топлива действительно могут способствовать достижению целевых уровней, намеченных на 2030 г. Однако если брать 2050 г. и позже, участники судоходной отрасли все чаще сходятся во мнении, что использовать полезные ископаемые в качестве бункерного топлива и при этом соблюдать нормы выбросов углерода будет невозможно. В качестве замены рассматриваются несколько вариантов, включая водород и аммиак. Последний приобретает особое значение, поскольку его можно сжигать как судовое топливо и использовать в топливных батареях на судах. У аммиака есть большое преимущество по сравнению с водородом, так как его намного легче хранить и перевозить, также можно транспортировать водород в виде аммиака. Кроме того, аммиак почти на 80% энергетически плотнее жидкого водорода.
Несколько компаний уже изучают возможность использования аммиака в судоходстве, хотя до новых требований IMO по выбросам углеводорода еще достаточно времени. В начале текущего года малайзийская судоходная компания MISC, Samsung Heavy Industries (SHI), Lloyd’s Register и MAN Energy Solutions объявили, что начали совместную работу над созданием танкера, использующего в качестве топлива аммиак. Норвежская нефтяная компания Equinor в партнерстве с морской технологической компанией Eidesvik намерены переоборудовать судно Viking Energy, чтобы к 2024 г. оно работало на аммиаке.
Компания Nordic Innovation объявила, что финансирует ряд проектов для создания экологически чистого судового топлива, включая Nordic Green Ammonia Powered Ships (NoGaps). Партнерами Nordic Innovation в этих проектах являются в том числе судоходная компания Lauritzen Kosan, а также Yara International. Целью данных исследований является создание работающего на аммиаке судового двигателя к 2025 г.
Судовладельцев интересует использование аммиака в качестве топлива не только на грузовых судах. Круизная компания Color Fantasy, чьи лайнеры курсируют между норвежским Осло и германским Килем, также собирается работать в этом направлении.
Датская каталитическая компания Haldor Topsoe готовит отчет для судостроительной и судоходной отраслей, где будет содержаться пошаговая инструкция, объясняющая, что потребуется для перехода на аммиак в качестве судового топлива. Кроме того, в данном отчете, как ожидается, будет уделено внимание имеющимся мощностям по хранению аммиака, например аммиачным резервуарам, которые можно использовать как бункеровочные хабы. Этот отчет, предположительно, выйдет позднее в 2020 г.
«Зеленый» аммиак — трудности производства
В отличие от обычного аммиака, который чаще всего производится из природного газа, «зеленый» аммиак выпускается следующим образом: сначала требуется энергия солнца, ветра или воды для производства электроэнергии, на которой работает электролизер для извлечения водорода из воды. При этом азот получают отдельно из воздуха, используя установку для разделения воздуха.
В качестве источника энергии аммиак в девять раз мощнее литиево-ионных батарей и почти в два раза энергетически плотнее жидкого водорода. При этом аммиак легче транспортировать, чем жидкий водород, используя имеющиеся технологии и инфраструктуру. Именно поэтому многие компании считают, что в будущем можно использовать аммиак как топливо, причем не только для получения энергии, но и для получения водорода, когда требуется именно водород.
Получение аммиака при помощи электролизера, работающего на возобновляемой энергии, — это не совсем новая концепция. Однако сейчас разрабатываются технологии для значительного увеличения ее энергоэффективности. Еще в начале 1900-х гг. норвежская компания Norsk Hydro вырабатывала аммиак, используя водную энергию. Компании в Северо-Западной Европе, а также в Японии, сейчас активно разрабатывают технологии для получения «зеленого» аммиака.
Крупных заводов, где производился бы «зеленый» аммиак, нет. В то же время и производители, и технологические компании начинают искать возможности для получения этого продукта более экологичным способом. Скорее всего, подобные предприятия придется строить в странах с избытком солнечной, ветряной или водной энергии, а идеально — с комбинацией как минимум двух этих источников энергии, чтобы уменьшить перебои в производстве и сократить издержки. Вдобавок этим предприятиям лучше находиться ближе к рынкам сбыта. Таким образом, среди возможных мест сразу выделяется Австралия с учетом ее возобновляемой энергии и географической близости к конечным потребителям в Восточной Азии.
Развитие технологий для получения «зеленого» аммиака
Ведущие компании в области технологий выработки аммиака стремятся найти способы использования возобновляемой энергии для получения аммиака и в то же время максимально увеличить энергоэффективность и сократить капитальные и операционные расходы.
Одна из таких компаний, Haldor Topsoe, разработала систему электролиза на твердооксидном топливе. Эта система использует возобновляемую энергию и производит исходный газ для выработки аммиака без разделения воздуха, что позволяет существенно уменьшить капитальные затраты. Пока это пилотный проект. Тем не менее уже ясно, что для работы данной системы потребуется на 10% меньше энергии, чем для работы обычной установки для выпуска аммиака из природного газа. Это поможет решить проблему слишком высоких эксплуатационных расходов при работе аммиачных агрегатов с использованием возобновляемой энергии. Строительство подобных установок потребует колоссальных первоначальных вложений. Следующая проблема — затратность и ограниченность источников возобновляемой энергии по сравнению с природным газом, которого много и который дешев. При текущих ценах на газ в Европе получение тонны «зеленого» аммиака обойдется примерно на 200—300% дороже, чем обычного. В более долгосрочной перспективе удешевление возобновляемой энергии, предположительно, позволит уменьшить эту разницу до 50—150%. Рост расходов на углеродные выбросы в Европе также может этому способствовать. Таким образом, ключевыми факторами для разработки технологий «зеленого» аммиака станут максимизация энергоэффективности и снижение цен на возобновляемую энергию.
Переход на «зеленый» аммиак потребует немало времени. Однако, признавая это, Пэт Хэн, руководитель научно-исследовательского подразделения в Haldor Topsoe, говорит, что очень важно предпринять первые шаги. С этой целью компания переходит от исследовательской фазы к этапу разработки: пилотная установка, работающая по технологии электролиза с использованием твердооксидного топлива, уже собрана. Финансировал создание этой установки консорциум датских компаний. Пилотный агрегат может вырабатывать 180 т/год «зеленого» аммиака. Следующий шаг — разработка технологии для коммерческого использования. В будущем Haldor Topsoe рассчитывает оснащать обычные аммиачные агрегаты, где используется природный газ, дополнительным оборудованием, которое позволит частично получать «зеленый» аммиак (сначала, к примеру, 10%, а потом увеличить эту долю). В этом случае нет необходимости строить новый завод, поскольку производители могут использовать имеющиеся мощности, нужно будет лишь добавить новый электролизер.
Данный подход может вызвать особый интерес у производителей в Западной Европе, которые могут использовать доступные им источники возобновляемой энергии и получать «зеленый» аммиак при минимальной себестоимости. Хотя за последние 30 лет в Западной Европе было построено мало новых агрегатов по выпуску аммиака, скорее всего, Европа станет одним из драйверов развития производства «зеленого» аммиака, если учесть, что, согласно плану Евросоюза на 2030 г. по климату и энергии, страны — члены Евросоюза должны сократить выбросы парниковых газов как минимум на 40% по сравнению с 1990 г.
Yara International пообещала уменьшить выбросы CO2 на 10% к 2025 г., а к 2050 г. намерена выйти на экологически чистое производство. К 2022 г. компания планирует заменить 10% своих мощностей по выпуску аммиака на юге Норвегии оборудованием для производства «зеленого» аммиака. К 2050 г. Yara собирается полностью выпускать аммиак на своем заводе в Порсгрунне по «зеленой» технологии. Над сокращением выбросов углерода Yara работает вместе с норвежской компанией Nel Hydrogen.
Даже компании, которые больше заняты в нефтегазовом секторе, начинают интересоваться «зеленым» аммиаком. Так, американская инженерно-строительная и сервисная компания KBR разрабатывает технологию K-GreeN solution для получения «зеленого» аммиака либо в отдельном электролизере, либо при помощи дополнительно устанавливаемого электролизера, в котором нет воздухоразделительной установки или контура синтеза.
Несколько более мелких компаний в Западной Европе и США разрабатывают инновационные способы, которые помогут буквально заново изобрести весь процесс производства аммиака. Некоторые из этих новых технологий обходятся без традиционного процесса Габера-Боша. Исландская компания Atmonia разрабатывает катализатор, который действует при атмосферном давлении и не нуждается в выделении водорода, поскольку задействует воду напрямую. При таком процессе выбросов CO2 не происходит. Кроме того, технология Atmonia позволяет без проблем останавливать производство и возобновлять его без особых затрат, а это, по словам Гудбьорг Рист, руководителя Atmonia, одно из главных преимуществ, когда речь идет о возобновляемой энергии, получаемой при помощи солнца и ветра. В настоящее время компания строит прототип катализатора, который позволит производить жидкий аммиак для использования в качестве удобрения. Однако конечной целью компании является производство безводного аммиака, сказала Гудбьорг Рист.
Компания Starfire Energy в штате Колорадо (США) разрабатывает модульные системы для выпуска аммиака без углеродных выбросов. Учитывая растущую потребность в возобновляемой энергии, которую можно хранить и использовать в качестве транспортного топлива и для отопления, компания считает аммиак идеальным выбором.
Starfire Energy отказалась от процесса Габера-Боша и создала систему, для работы которой не требуется столь высокого давления. Этот реактор подстраивается под уровень ветряной и солнечной энергии, обходясь без ископаемого топлива для получения аммиака. Компания начала с прототипа Rapid Ramp NH3 мощностью 3 кг/сут. и теперь строит реактор мощностью 10 кг/сут. После этого Starfire Energy сможет перейти к созданию пилотной модульной системы мощностью 100 кг/сут. Мощность второго пилотного реактора заложена на уровне 1 т/сут. Затем мощность одной установки будет увеличена до 50 т/сут. На одной площадке можно будет устанавливать 10 реакторов, совокупная мощность которых будет достигать 500 т/сут. Дженнифер Бич, сооснователь и исполнительный директор Starfire Energy, сообщила, что 80% оборудования будет изготавливаться фабричным способом, а 20% — будет построено на площадке.
Цель Starfire Energy состоит не только в том, чтобы производить аммиак без углеродных выбросов, но и подстроиться под его конечное использование. Компания работает над более низкотемпературным катализатором крекинга аммиака, который позволяет превращать аммиак в азот и газообразный водород. Затем этот азот и водород можно использовать одновременно либо задействовать один только водород как источник энергии для автомобилей и предприятий, где требуется хранящийся под высоким давлением водород для топливных элементов.
На этой неделе я решил посмотреть, что происходит в методах хранения и использования водорода. Одна из тем с которой я пересекся это использования аммиака, как метода работы с водородом.
В этой статье поговорим о том, в чем “засмес”, какие есть подводные камни и есть ли какие-то стартапы и компании, которые решают проблему в контексте устойчивого развития.
Что такого с водородом?
Вся история с водородом очень проста: если вы сжигаете водород, то вы получаете в качестве выхлопа воду (2H2 + О2 = 2Н2О) и тепло от сгорания.
Нет выхлопа улгекислого газа и любых других вредных газов.
Выделяется много тепла на единицу массы. Удельная теплота сгорания примерно 140 Мдж на кг (у бензина около 40-45 МДж на кг).
Водород хорошо распространен в природе в форме соединений (в углеводородах и воде, например).
Водород занимает очень большой объем при комнатной температуре и атмосферном давлении, из-за этого на единицу объема у него очень маленькая энергоемоксть. При комнатных условиях в 1 литре водорода всего 0.08 грамм. Для практического применения его надо сжижать (-252 градуса), тогда его плотность увеличивается до примерно 70 грамм на литр. Сравните с 780 граммами на литр для бензина. В итоге бак на 100 литров водорода в криогенном состоянии (под -252 градусами) будет содержать примерно в 3 раза меньше энергии, чем бензиновый.
Криогеника означает усложнение хранения и транспортировке и затраты за сжижение (довольно сложное сжижение до низких температур), а так же контроль за давлением.
Водород является самым маленьким атомом и в газообразном виде имеет тенденцию проникать сквозь любые стенки, он пролезает через другие молекулы. Те водород медленно утекает даже из закрытого баллона через стенки.
Водород горит и образует взрывоопасную смесь с воздухом.
Существует 3 основных промышленных способа производства водорода -
Метановая конверсия паром подразумевает “обработку” метана в парах воды под высокой температурой и давлением. Таким образом получается относительно дешевый водород, одна проблема, на выходе мы имеем СО2. Весь цикл оказывается таковым, что проще было просто сжечь метан, получили бы меньше выхлопов углекислого газа. Сейчас более 75% объемов производства водорода делается таким образом. Большая надежда нефтегазовой отрасли состоит в том, чтобы делать водород именно таким образом и объявлять себя зелеными. Некоторые из нефтяников и газовиков на этом фоне хотят развивать технологии улавливания СО2 из результатов производства водорода и закачивания его обратно в пласт откуда взяли метан. Теоретически мы можем это СО2 там заблокировать на миллионы лет. Но возможно он все равно будет оттуда утекать.
Продувка водяного пара над раскаленным коксом. В целом идея так же, что и конверсией метана. На выходе углекислый газ и водород. В такой цепочке опять же это никакой не зеленый водород.
Электролиз. Это разложение воды на водород и кислород при помощи электричества. Сейчас на этот способ приходится 4% от объема производства водорода. Если электричество было добыто с низким углеродным следом, то и водород такой будет с низким углеродным следом.
Сейчас водород больше используется не как топливо, а как часть промышленной химии. Те пока эра водородной энергетики это какое-то возможное будущее. Но тк давление растет и есть отрасли, где очень трудно заменить ископаемое топливо, то на водород смотрят все больше, как на энергетическое топливо
При чем же тут аммиак
Аммиак это соединение 3 атомов водорода и азота. Особенность в том, что в таком виде водород “плотнее” упакован. Аммиак проще сжижается (при -36 градусах) и имеет более высокую плотность как газ (20 грамм на литр) и особенно как жидкость (680 грамм на литр, почти как бензин). А значит его проще сжижать и проще прокачивать в трубопроводах.
При сжигании аммиака в идеале можно получить только воду и азот. Правда сжигать аммиак довольно не просто, это требует специального механизма смешения с воздухом, присутствия катализаторов и контроля за образованием оксидов азота, которые ядовиты для людей. При этом аммиак выделяет не слишком много темпа на кг (18 Мдж на кг). Тогда в нашем сравнении с бензином аммиак лучше чистого водорода на 25-30%.
Другой вариант это использовать аммиак именно так механизм транспортировки водорода.
Но 80% аммиака на самом деле идет на производство удобрений, так что получение “зеленого” аммика” это и способ снизить углеродоемкость пищевой промышленности.
Промышленный метод производства аммиака сегодня это процесс Хабер-Бош, когда водород смешивают с азотом под высоким давлением и температурой в присутствии катализаторов. Процесс требует поддержания стабильным параметров и поэтому его трудно реализовать в рамках переменной мощности от возобновляемых источников.
Если бы могли найти иной дешевый способ генерации аммиака каким-то образом напрямую из воды и без процесса Хабер-Бош, мы могли бы получать готовый к транспортировке “зеленый” аммиак и затем и водород (через разложение аммиака).
В итоге интерес к аммиаку есть с трех направлений:
Зеленый аммиак для удобрений.
Аммиак как топливо в судах. Именно они сильнее всего рассматривают возможности аммиака и по первым прикидкам это более оптимальное решение, чем батереи или чем чистый водород. Для требуемого объема запаса энергии батареи слишком тяжелые, а чистый водород занимает слишком много места. Аммиак хуже, чем обычном топливо, но во всяком случае баки под него не слишком тяжелые, и занимают разумный объем судна.
Метод транспортировки самого водорода из мест его производства.
Project HEGRA - проект в Норвегии по электрификации процесса производства аммика и полном функционировании на зеленой энергии. Это завод на 400 тыс тонн аммика в год. Довольно крупный проект.
Бизнесы связанные с проектом HEGRA (компания - wartsila) так же исследуют возможности использования аммика в двигателях внутреннего сгорания, а так же использования аммика в топливных ячейках. Пока результаты это общие слова.
Amogy - Ничего конкретного. Даже нечего обсуждать, просто рекламная страничка.
Jupiterionics - Идея базируется на электрохимическом производстве аммиака. Они базируют свою работу на прорыве в области электрохимического прямого производства аммиака. Между двумя электродами помещают смесь водорода, Li3N и специального обменного носителя. Под действием электрического тока, водород скапливается около отрицательного электрода, а Li3N у положительного. Носитель сначала имеет отрицательный заряд и мигрирует к Li3N, там происходит обмен атома водорода в носителе на атом лития. Носитель после этого мигрирует к отрицательному электроду, где производит обратный обмен, литий заменяется на водород. В итоге мы последовательно заменяем весь литий в соединении Li3N на водород и получаем NH3 (аммиак). По заявлению создателей этот процесс происходит гораздо быстрее, чем аналогичные методы электролиза и позволяет избежать процесса Хабер-Бош. Для меня правда вопросы остаются в том, откуда они берут водород в самом начале. В итоге все это базируется на зеленом способе производитель электроэнергию. Но с другой стороны, если будет много дешевой энергии, то и процесс Хабер-Бош можно организовать на зеленой энергии, а стабильность снабжения обеспечить батареями. Стартап получил 2.65 млн австралийских долларов на развитие проекта и идеи в марте 2021 года.
Seaborg Technologies - хотят использовать ядерные реакторы на расплавах солей, размещенные на кораблях для производства водорода и аммиака. Хотя основной фокус просто на баржах с ядерными реакторами, как проект Академик Ломоносов.
Kapsom - фирма занимающаяся строительством химических заводов объявила, что сделала первый завод по зеленому аммиаку в Индии на 1500 тонн аммиака в год в 2020 году. Это конечно гораздо скромнее, чем 400 тыс тонн по проекту HERGA.
Yara - один из крупнейших производителей аммиака (и один из участников проекта HERGA) в апреле 2022 заказали 15 плавающих аммиачных терминала, как основу будущей системы заправки судов аммиаков. Это еще один признак большого изменения в индустрии. В рамках этого проекта Yara планирует сделать аммиак доступным для судов топливом к 2024 году.
Выводы:
Пока аммиак как топливо выглядит как интересная идея, основной потенциал сосредоточен просто в “озеленении” производства обычного аммиака. Именно в этом направлении видны объемные инвестиции и реальный бизнес. Стоит ожидать, что там, где производят водород методом электролиза будет появляться и места производства аммиака.
Нам как инвесторам доступны компании работающие в этой области (wartsila, например есть на бирже), но сами стартапы пока на такой стадии, что обычного инвестору туда не войти.
От всей темы остается ощущение, что может быть много хайпа, но основной объем производства все равно будет связан со старым и скучным электролизом. Хотя на самом деле он не скучный, тк технология эффективного электролиза еще далека от совершенства и реальные затраты энергии значительно выше, чем теоретический минимум необходимый для разделения молекул.
Ежегодно сотни миллионов тонн CO2 выбрасываются морским транспортом, нанося серьезный вред климату. В то время как ученые всего мира испытывают новые двигательные установки, способные заменить мазут на судах, исследователи университета Фраунгофера работают в рамках международного консорциума по разработке топливных элементов на основе аммиака.
При использовании аммиака в качестве топлива для судов с электрическими двигателями, он не уступает по экологичности водороду, но при этом проще и безопаснее в обращении.
Преимущества аммиака как топлива
В настоящее время водород находится в центре внимания в области устойчивой энергетики: существуют планы по использованию водорода в качестве топлива для автобусов, коммерческого транспорта и даже автомобилей. Однако Институт микроинженерии и микросистем IMM им. Фраунгофера в Майнце работает над еще одной перспективной возможностью. В рамках проекта ShipFC Институт Фраунгофера сотрудничает с 13 европейскими партнерами по консорциуму с целью разработки первого в мире топливного элемента на основе аммиака для судоходства. Исследователи Фраунгофера отвечают за разработку каталитического нейтрализатора, предотвращающего образование выбросов, которые могли бы нанести вред климату.
Морской транспорт является основным источником выбросов парниковых газов. Согласно информации, предоставленной Немецким агентством по охране окружающей среды (UBA), в настоящее время на долю морского транспорта в мировом океане приходится около 2,6 % выбросов CO2. В 2015 году было выброшено около 932 миллионов тонн CO2, и эта цифра увеличивается с каждым годом. Очевидно, что необходимы срочные контрмеры.
Проект ShipFC призван доказать, что новая безэмиссионная двигательная технология работает безопасно, надежно и бесперебойно даже на больших судах и в длительных плаваниях. Проект координируется норвежской организацией NCE Maritime Cleantech, целью которой является разработка экологически чистых технологий в морском секторе.
Аммиак известен, прежде всего, как удобрение в сельском хозяйстве. Однако он может также функционировать в качестве высококачественного энергоносителя. Профессор Гюнтер Кольб (Gunther Kolb), директор энергетического подразделения и заместитель директора института IMM, объясняет: "Аммиак имеет значительные преимущества перед водородом. Водород должен храниться при температуре -253 градуса Цельсия в жидком виде или при давлении около 700 бар в виде газа. Жидкий аммиак можно хранить при разумной температуре -33 градуса Цельсия при стандартном давлении и +20 градусов при 9 бар. Это значительно облегчает и упрощает хранение и транспортировку данного энергоносителя".
Процесс производства электроэнергии из аммиака функционирует аналогично электростанциям на основе водорода. Сначала аммиак (NH3) подается в реактор деления, где он разделяется на азот (N2) и водород (H2). 75 % газа состоит из водорода. Небольшое количество аммиака (NH3, 100 ppm) не преобразуется и остается в газовом потоке.
Во-вторых, азот и водород подаются в топливный элемент, в него вводится воздух, что позволяет водороду гореть и образовывать воду. При этом вырабатывается электрическая энергия. Однако водород не полностью преобразуется в топливном элементе. Около 12 % водорода и некоторое количество остаточного аммиака оставляют топливный элемент несгоревшим. Этот остаток затем подается в катализатор, разработанный компанией Fraunhofer IMM. Здесь поступает воздух, и остаток контактирует с гофрированной металлической фольгой, покрытой порошковым слоем каталитических частиц, содержащих платину. Это вызывает химическую реакцию. В конечном итоге, единственными конечными продуктами являются вода и азот. Оптимальный процесс реакции не приведет даже к образованию экологически вредных оксидов азота.
Группа исследователей IMM также разрабатывает реактор, содержащий катализатор, который работает пассивно. Реактор контролирует температуру и поток газа. Например, он подогревает катализатор еще до того, как двигатели запустятся, так как он менее эффективен в холодное время года. "Температура газов, проходящих через каталитический нейтрализатор, должна быть, вероятно, около 500 градусов Цельсия, чтобы процесс очистки отработанных газов был как можно более эффективным", - объясняет Кольб.
Исследователи IMM из Фраунгофера имеют многолетний опыт разработки реакторов, в том числе катализаторов для самых разных областей применения в сфере транспорта и мобильности. Институт в Майнце располагает девятью испытательными установками, но очистка отработанного газа от аммиачных топливных элементов мощностью 2 мегаватт до сих пор является технологической проблемой. "Мы должны развивать нашу существующую технологию работы на аммиачных топливных элементах дальше, и каталитический нейтрализатор для судна, очевидно, намного больше, чем обычный двигатель", - говорит Кольб.
Команда IMM планирует закончить работу над первоначальным, небольшим прототипом к концу 2021 года, за которым последует прототип фактического размера к концу 2022 года.
Во второй половине 2023 года первый корабль с топливным элементом, работающим на аммиаке, выйдет в море - " Энергия викингов", судно снабжения, принадлежащее норвежской судоходной компании " Eidesvik ". После этого другие типы судов, например, грузовые суда, будут оборудованы топливными элементами, работающими на аммиаке.
Аммиак поставляется компанией YARA, партнером в консорциуме ShipFC. В настоящее время химическая компания производит треть аммиака, используемого во всем мире. В проекте ShipFC используется "зеленый" аммиак, то есть аммиак, получаемый из возобновляемых источников энергии.
ShipFC открывает большие возможности для ранее недооцененного энергоносителя. Исследователь IMM Гюнтер Колб (Gunther Kolb) подробно останавливается на этом: "Мы рассматриваем аммиак не как непосредственного конкурента водорода, а как дополнительную опцию в области устойчивой энергетики. С его преимуществами в области хранения, эта экологически чистая технология производства электроэнергии, безусловно, играет свою роль". Использование ее на судах - это только начало".
Понравилась статья? Напишите свое мнение в комментариях.
Подпишитесь на наш ФБ:
Доля морского транспорта в общем потреблении топлива составляет около 11% (примерно 10 млн барр./сут.). Но не менее важно, что в нынешней ситуации соревнования между альтернативными видами топлива суда во многом задают тренд в пользу того или иного вида горючего. Значительные объемы потребления оправдывают массовое производство, строительство топливных баз и инфраструктуры в целом, тем самым подсказывая, на какое топливо делать ставку в остальных сегментах рынка.
Капля в море
Компания DNV GL приводит данные о судах, которые вынуждены соблюдать обязательства по сокращению выбросов серы или решили использовать альтернативное топливо в расчете на будущее.
В документе приводится также структура флота, использующего альтернативные источники энергии. Аккумуляторы используют пассажирские и вспомогательные суда, изредка рыболовные. Океанские танкеры и контейнеровозы ориентируются на СПГ, а суда, перевозящие химикаты, могут выбрать и метанол.
Учитывая, что всего в мире насчитывается порядка 95 тыс. торговых судов, 414 судов на СПГ составляют всего лишь 0,4% мирового торгового флота. Так что исход сражения между видами топлив за бункеровку судов до конца не определен.
Мал золотник…
Хотя судов, использующих альтернативное топливо, всего чуть больше тысячи, мировые порты ускоренно строят инфраструктуру для их обслуживания.
Среди жидких топлив в портах, по данным агентства ICIS, представлены: биодизель, аммиак, метанол, LPG, бункеровочное топливо с 3,5% серы, СПГ (расположены по убыванию цены на данный момент).
Пока СПГ и сернистый мазут выигрывают по цене у всех конкурентов, но это не значит, что СПГ останется лидером на долгое время. Недавний трех-четырехкратный взлет цен неизбежно вынудит судовладельцев задуматься: стоит ли делать ставку на газ.
Но еще больше газу угрожает углеродобесие. При сжигании газа выделяется СО2, поэтому адепты устойчивого развития хотят найти замену не только нефти, но и газу. В недавнем докладе The First Wave. A blueprint for commercial-scale zero-emission shipping pilots «Комиссии по переходу на новые виды энергии» в партнерстве с Коалицией «В направлении к нулю» был представлен анализ наиболее перспективных видов топлива для морского транспорта с точки зрения технической и экономической возможности достижения нулевых выбросов.
Биотопливо
Некоторые виды морского топлива на основе биомассы могут использоваться непосредственно в существующих двигателях и топливной инфраструктуре, что исключает необходимость каких-либо инвестиций в новые двигательные установки, пишут авторы. Многие виды биотоплива близки к паритету затрат с HFO (Heavy Fuel Oil, тяжелое судовое топливо, обычно мазут). Биотопливо при сгорании выделяет СО2, но согласно канонам «зеленой» религии до этого растения, из которых оно производится, поглотили этот самый углерод из атмосферы.
Основной вид биотоплива — этанол, получаемый из любых растений, содержащих сахара и крахмал. Ставку на этанол как топливо для автомобилей в 70-х годах сделала Бразилия, в которой хорошо растет сахарный тростник, плантациями которого занято 4,5% площади страны. На него приходится почти 50% всего потребления топлива, и автомобили ездят либо на бензине с 20% этанола, либо на чистом этаноле, который заметно дешевле бензина.
У этанола три проблемы — техническая, масштабируемости и этическая.
Обычный бензин можно в любых пропорциях разводить этанолом, но чем больше этанола, тем меньше мощность, потому что у этанола на 34% меньше теплота сгорания. Двигатели для чистого этанола работают почти как бензиновые за счет большей степени сжатия (у этанола октановое число 105).
В мире используются разные смеси бензина с этанолом. В США, например, НПЗ должны добавлять в топливо 10% этанола, за соблюдением чего старательно следят его производители, а нефтяники, в свою очередь, через суды пытаются от этой обязанности уклониться. При такой концентрации топливо можно использовать в обычном бензиновом двигателе.
В Швеции продается топливо Е85 — смесь 85% этанола с бензином.
Второй вопрос – откуда брать столько этанола? Есть оценки, что даже при стопроцентной эффективности процесса переработки сырья в спирт для того, чтобы только США могли перевести с нефти на этанол весь транспорт, нужно 75% сельскохозяйственных земель нашей планеты засеять соответствующими культурами.
На этическую сторону вопроса указывают гуманисты – аморально переводить зерно в топливо, когда столько людей на планете недоедают.
Синтетическое дизельное топливо
Для производства синтетического дизельного топлива в реакторах используют комбинацию водорода и СО (так описывают это авторы доклада). Его можно использовать с обычными двигателями. Для достижения нулевого выброса при использовании производство синтетического дизельного топлива должно сопровождаться захоронением углерода.
Однако технология производства синтетического дизельного топлива все еще находится на стадии исследований, говорится в документе. По мнению авторов, она будет коммерчески доступна только к 2030 году. К тому же при производстве такого топлива требуется много энергии и высокие начальные капитальные затраты.
Водород
Потенциально водород может использоваться как топливо для судов. Авторы утверждают, что значительное снижение затрат на производство водорода с нулевым содержанием углерода ожидается в ближайшие 10–15 лет благодаря развитию глобальной водородной экономики. Однако прямое использование водорода на глубоководных судах — в двигателях внутреннего сгорания, либо в топливных элементах в сочетании с электрическими двигателями — создает проблемы, связанные с его низкой объемной плотностью. Для дальнего рейса для хранения водорода потребуется слишком большой физический объем.
Наземный транспорт сейчас усиленно пытаются перевести на водород, но получается это только в государственном сегменте, когда высокие расходы на инфраструктуру и двигатели ложатся на бюджет.
В Германии, которая может претендовать на звание лидера в Европе по водородным технологиям, в 2020 году на дорогах страны было всего 49 водородных автобусов и один большегрузный грузовик, а также 979 легковых автомобилей (по данным компании H2 Mobility, которая занимается инфраструктурой и производством водородного топлива).
Спрос пока остается минимальным, на 90 действующих станций в сутки приходится в среднем 1,2 заправки. До сих пор нет даже стандарта на давление водородных баллонов — 350, 500 или 700 атмосфер.
Не считая Германии, в Европе всего десять водородных заправочных станций для грузовиков и автобусов — три в Нидерландах и по одной в Шотландии, Бельгии, Франции, Испании, Швейцарии, Италии и Чехии. Да, одно дело рисовать планы и графики, другое — заставить частный бизнес многократно переплачивать за климатическое безумие.
Аммиак
Аммиак, полученный из зеленого или синего водорода, будет иметь более высокую объемную плотность и относительную легкость хранения по сравнению с водородом, и поэтому может представлять собой более легко развертываемый вариант для глубоководных судов. Однако он по-прежнему потребует значительных инвестиций в двигатели, бункеровку и топливную инфраструктуру, будет иметь более низкую объемную плотность, чем мазут, а также потребует новых правил безопасности и обращения с ним для использования в качестве судового топлива из-за его токсичности.
Сегодня стоимость зеленого аммиака примерно в два с половиной раза превышает стоимость обычного HFO, а если сделать поправку на плотность энергии, то зеленый аммиак обойдется примерно в пять раз выше стоимости HFO.
Кроме того, хотя аммиачные двигательные установки находятся в процессе разработки, в настоящее время они не являются коммерчески доступными.
Использование аммиака для наземного транспорта, наверное, можно считать закрытой темой, слишком опасны его утечки, а резкий запах не удастся убрать из-за высокой летучести соединения. Аммиак — вещество для химической промышленности.
Метанол
Метанол, полученный из комбинации водорода и CO или CO2, может быть более легко доступен, чем зеленый или синий аммиак в краткосрочной перспективе, поскольку двойные двигатели на метаноле-HFO уже доступны в продаже. Вполне вероятно, что нормативная база Международной морской организации (ИМО) для использования его на судах в качестве топлива будет стандартизирована и утверждена в начале 2021 года, считают авторы доклада.
Как и биотопливо, метанол выделяет CO2 в процессе сжигания, поэтому в цепочку производства-потребления надо вставлять захват СО2 из атмосферы или поглощение СО2 каким-либо способом. Наиболее очевидный выход — покупка зеленых сертификатов, современных индульгенций на прощение углеродных грехов.
Менее 1% мирового флота работает на альтернативных видах топлива
По данным компании DNV GL на сегодня менее 1% существующего мирового парка судов работает на альтернативных видах топлива, в то время как 10% судов заказываются с альтернативными топливными системами.
В докладе рассматриваются три варианта отношения к декарбонизации:
- никакой дальнейшей декарбонизации;
- реализация амбиций ИМО – сокращение выбросов парниковых газов как минимум на 50% к 2050 году;
- полное обезуглероживание судоходства к 2040 году.
В сценариях без амбиций по декарбонизации преобладают мазут с очень низким содержанием серы, судовой газойль и СПГ. Но в двух других вариантах к 2050 году различные виды углеродно-нейтрального топлива будут занимать от 60% до 100% доли рынка.
Ископаемый СПГ будет занимать значительную долю рынка до тех пор, пока правила не будут ужесточены в 2030 или 2040 году, считают авторы.
Метанол как топливо для судов и автомобилей
С точки зрения возможной замены нефтепродуктов в направлении движения к декарбонизации все чаще рассматривается метанол, у которого несколько достоинств:
- легко получается из природного газа и другого сырья, в частности, из дерева и растений;
- применяется для производства широкого спектра химической продукции, то есть всегда имеется в наличии в достаточных объемах;
- в отличие от газообразных топлив его можно хранить в стальных резервуарах при атмосферном давлении;
- его использование не требует принципиальной переделки мотора.
- в несколько раз более ядовит, чем бензин;
- плохо воздействует на резину и пластики;
- вызывает коррозию алюминия;
- накапливает воду, образуя гель;
- имеет низкую испаряемость при отрицательных температурах, поэтому двигатели лучше заводятся, когда в метаноле есть какой-то процент бензина.
В декабре прошлого года канадская компания Waterfront Shipping Company (WFS) объявила о постройке восьми новых танкеров на метиловом спирте, которые получит в 2021–2023 году. WFS совместно с партнерами еще в 2016 году запустила первые три танкера-химовоза на метаноле, сегодня в ее парке уже 7 таких судов.
В мире растет интерес к метанолу, как альтернативе традиционному бункерному топливу. Многие судовладельцы стали рассматривает метанол в качестве «чистой» замены нефтепродуктам. «Основной сегодняшний аргумент в пользу метанольных проектов — возможности использования метанола в качестве компонента судового топлива, — подтверждает Фарес Кильзие, глава инвестиционного фонда CREON Capital. — Международная морская организация (IMO) последовательно реализует курс на отказ от высокосернистого судового топлива типа мазута, в качестве альтернатив которому рассматриваются либо СПГ, либо метанол — основной его конкурент».
Индийская угольная компания Coal India Ltd (CIL) в сентябре объявила международный тендер на участие в создании первого в Индии завода по переработке угля в метанол. На заводе планируется производить около 6,76 млн т метанола в год, который будет использоваться для смешивания с бензином в концентрации до 15%.
В Китае, производящем из угля более половины мирового метанола, он в негазифицированных домах используется для отопления и для кухонных плит, В 2020 году в Китае на каждый из этих сегментов уйдет около 4 млн тонн метанола.
Суммарно на все топливные сегменты приходится 17% от 85 млн т/г глобального производства метанола.
На сегодня, после падения цен на нефть и взлета цен на метанол, он как топливо дороже даже низкосернистой нефти, но при усугублении требований на выбросы SOx и NOx метанол становится привлекательным на длительную перспективу как основное топливо или в смеси с нефтепродуктами.
Динамика стоимости метанола ($/ГДж) в сравнении с другими топливами для бункеровки
Метанол также рассматривается как замена водороду в зеленой энергетике. Схема выглядит так: электроэнергия с ВЭС или СЭС идет на производство зеленого водорода, который тут же используется для производства метанола. В такой схеме отпадает необходимость в водородной инфраструктуре, а хранить метанол и обращаться с ним гораздо проще, чем с водородом.
В крайнем случае, если практика покажет опасность массовой работы с метанолом, его можно превратить в этиловый спирт в реакции с синтез-газом.
В настоящее время удалось достичь селективности реакции по этанолу 90%. Упорные слухи, что в СССР так и делалась дешевая водка-«табуретовка», даже нашли отражение в известной песне Владимира Высоцкого: «а если б водку гнать не из опилок, чего б нам было с пяти бутылок».
Мировое производство метанола растет примерно на 6,5% в год.
В 2019 году в России было произведено 4,46 млн тонн метанола. В целом, за период с 2015 по 2019 год прирост мощностей составил почти 1 млн т. Половина метанола идет на экспорт.
Недавняя новость — трансформация новыми владельцами проекта «Печора СПГ» в метанольный (полгода назад новый владелец ЯТЭК сделал ровно наоборот — перевёл метанольный в СПГ-проект). Даже первая линия «метанольной Печоры» — это 1,7 млн т, т.е. почти удвоение действующих экспортных объёмов в случае реализации.
Двадцатилетний контракт на поставку метанола в Японию заключила компания, которая реализует проект строительства завода в городе Сковородино. Соглашение стало первым долгосрочным в России на сбыт еще не произведенной спиртовой продукции, сообщает правительство области. Договоренность предполагает поставки метанола в страну Восходящего солнца в объеме полмиллиона тонн в год. Сырьем для будущего производства станет природный газ, поставляемый по трубопроводу «Сила Сибири».
Активное строительство завода в городе Сковородино начнется в 2021. Первая продукция должна сойти с линий через четыре года.
В программном интервью РБК вице-премьер Александр Новак особо отметил развитие в России метанольного производства. «Это очень высокие темпы [рост мирового рынка на 6,5% в год], и перспективы тоже есть большие. Особенно в Азиатско-Тихоокеанском регионе. Мы на сегодняшний день занимаем очень маленькую нишу», – подчеркнул Новак. По его словам, Россия могла бы в ближайшем будущем занять долю рынка в 10-15%, тогда как сейчас занимает порядка 5%.
Заключение
По совокупности свойств у нефти и нефтепродуктов нет конкурентов на мировом рынке. Но регулярные информационные вбросы «нефть кончается» и углеродобесие стимулирует попытки найти замену нефти в качестве топлива и сырья для химической промышленности. Наиболее очевидные кандидаты на такую замену – этанол и метанол.
У метанола при всех его недостатках имеется огромное преимущество: практически неиссякаемый источник дешевого сырья – любая органика. Когда-то нефть вытеснила целлюлозу из производственных цепочек, но люди старшего поколения еще помнят фотопленки, столовые наборы и прочую продукцию из целлюлозы.
Из метанола сегодня выпускается широкий спектр химической продукции.
При выборе метанола в качестве топлива или его компонента, у потребителя не будет проблем с его наличием на рынке.
Ситуация открывает предпосылки, как сказано в отчете «Восток Капитал», к «взрывному росту экспорта российского метанола». Министерством промышленности и торговли разработана стратегия развития химического и нефтехимического комплекса до 2030 года, в которой производству метилового спирта отведено особое место. В России запланирована реализация не менее 15 проектов по производству метанола с общим объемом продукции более 19 млн тонн, что приведет к увеличению суммарной мощности в пять раз. Хотя вряд ли все проекты будут реализованы,
Для рынка нефти и нефтепродуктов принципиально появление реальной альтернативы. Замена даже 10-15% нефти на метанол и его продукты может уронить цены на нефть, что показала весна-лето 2020 года. В любом случае, наступление метанола не даст биржевым спекулянтам поднять цены на нефть до $150, что, может быть, даже хорошо.
Автор статьи
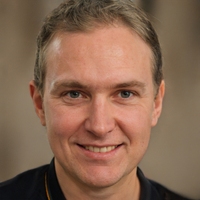
Читайте также:
- Презентация права и обязанности государства и граждан по обеспечению безопасности жизнедеятельности
- Определение места жительства ребенка судебная практика
- Суд канады признал что ковида нет
- Что такое досудебная пробация
- Письменные и вещественные доказательства которые невозможно или затруднительно доставить в суд