Кто осуществляет контроль качества сварных соединений в сосудах
Обновлено: 02.05.2024
7.1.1. Контроль качества работ по изготовлению и монтажу конструкций резервуаров должен осуществляться заказчиком, изготовителем и монтажником (производителем работ).
7.1.2. Проектировщик осуществляет авторский надзор за сооружением резервуаров. Представителям заказчика, а также представителям проектной организации, выполняющим авторский надзор, представляются свободный доступ ко всем рабочим местам, где выполняются работы по изготовлению и монтажу конструкций резервуаров, и рабочая документация.
7.1.3. При сооружении резервуаров применяются следующие виды контроля качества сварных соединений:
- механические испытания сварных соединений образцов-свидетелей;
- визуальный контроль всех сварных соединений резервуара;
- измерительный с помощью шаблонов, линеек, отвесов, геодезических приборов и т.д.;
- контроль герметичности (непроницаемости) сварных швов с пользованием проб «мел-керосин», вакуумных камер, избыточного давления воздуха или цветной дефектоскопии;
- физические методы - для выявления наличия внутренних дефектов: радиография или ультразвуковая дефектоскопия, а для контроля наличия поверхностных дефектов с малым раскрытием - магнитография или цветная дефектоскопия;
- гидравлические и пневматические прочностные испытания конструкции резервуара.
7.2. Организация контроля
7.2.1. В проектной документации (ППР) должны указываются методы и объемы контроля всех сварных соединений конструкций резервуара, нормативы для оценки дефектности сварных швов и последовательность работ.
7.2.2. Ответственность за организацию контроля качества сварных соединений, как правило, возлагается на руководителей сварочных работ от изготовителя и монтажника.
7.2.3. Контроль качества сварных соединений резервуаров физическими методами выполняется по заявке, в которой должны быть указаны характеристики соединения, тип и категория шва, толщина металла и марка стали, пространственное положение, объем контроля.
7.3. Визуальный контроль
7.3.1. Визуальному контролю должны подвергаться 100 % длины всех сварных соединений резервуара.
7.3.2. По внешнему виду сварные швы должны удовлетворять следующим требованиям:
- по форме и размерам швы должны соответствовать проекту;
- швы должны иметь гладкую или равномерно чешуйчатую поверхность (высота или глубина впадин не должка превышать 1 мм);
- металл шва должен иметь плавное сопряжение с основным металлом;
- швы не должны иметь недопустимых внешних дефектов.
7.3.3. К недопустимым внешним дефектам сварных соединений резервуарных конструкций относятся трещины любых видов и размеров, несплавления, наплывы, грубая чешуйчатость, наружные поры и цепочки пор, прожоги и свищи.
Подрезы основного металла допускаются не более величин, указанных в табл. 7.1.
Таблица 7.1
Примечание. Длина подреза не должна превышать 10 % длины шва.
7.3.4. Выпуклость швов стыковых соединений не должна превышать значений, указанных в табл. 7.2.
Таблица 7.2
7.3.5. Для стыковых соединений из деталей одной толщины допускается смещение свариваемых кромок относительно друг друга, не более:
- для деталей толщиной до 10 мм - 1,0 мм;
- для деталей толщиной более 10 мм - 10 % толщины, но не более 3 мм.
7.3.6. Выпуклость или вогнутость углового шва не должна превышать более чем на 20 % величину катета шва.
7.3.7. Уменьшение катета углового шва допускается не более 1 мм. Увеличение катета углового шва допускается не более следующих значений:
- для катетов до 5 мм - 1,0 мм;
- для катетов свыше 5 мм - 2,0 мм.
7.3.8. В местах пересечения сварных швов и в местах исправления дефектов необходимо обеспечивать минимальную концентрацию напряжений за счет обеспечения плавного сопряжения шва с основным металлом.
7.4. Контроль герметичности
7.4.1. Контролю на герметичность подлежат все сварные швы, обеспечивающие герметичность резервуара, а также плавучесть и герметичность понтона или плавающей крыши.
7.4.2. Контроль герметичности сварных швов с использованием пробы «мел-керосин» следует производить путем обильного смачивания швов керосином. На противоположной стороне сварного шва, предварительно покрытой водной суспензией мела или каолина, не должно появляться пятен. Продолжительность контроля капиллярным методом зависит от толщины металла, типа сварного шва и температуры испытания. Заключение о наличии в сварном соединении сквозных дефектов делается не ранее 1 ч после нанесения на шов индикатора сквозных и поверхностных дефектов.
7.4.3. При вакуумном способе контроля герметичности сварных швов вакуумкамеры должны создавать разрежение над контролируемым участком с перепадом давления не менее 250 мм вод. ст. Перепад давления должен проверяться вакуумметром. Неплотность сварного шва обнаруживается по образованию пузырьков в нанесенном на сварное соединение мыльном или другом пенообразующем растворе.
7.4.4. Допускается не производить контроль на герметичность стыковых соединений листов стенки толщиной 12 мм и более.
7.4.5. Контроль давлением применяется для проверки герметичности сварных швов приварки усиливающих листовых накладок люков и патрубков на стенке резервуаров. Контроль производится путем создания избыточного воздушного давления от 400 до 4000 мм вод. ст. в зазоре между стенкой резервуара и усиливающей накладкой с использованием для этого контрольного отверстия в усиливающей накладке. При этом на сварные швы внутри и снаружи резервуара должна быть нанесена мыльная пленка, пленка льняного масла или другого пенообразующего вещества, позволяющего обнаружить утечки. После проведения испытаний контрольное отверстие должно быть заполнено ингибитором коррозии.
7.4.6. Контроль герметичности сварных соединений настила крыш резервуаров рекомендуется проводить в процессе гидравлических и пневматических испытаний за счет создания избыточного давления воздуха внутри резервуара до 150 ÷ 200 мм вод. ст.
7.5. Физические методы контроля
7.5.1. Объем контроля сварных соединений резервуаров физическими методами определяется в рабочей документации КМ в зависимости от:
- класса резервуара по степени опасности;
- категории сварного шва;
- уровня расчетных напряжений в сварном соединении;
- условий и режима эксплуатации резервуара, включая температуру эксплуатации, цикличность нагружения, сейсмичность района и т.д.
7.5.2. Контроль радиографический.
7.5.2.1. Контроль радиографический (рентгенографированием или гаммаграфированием) должен производиться в соответствии с нормативными документами, утвержденными в установленном порядке, для всех резервуаров объемом 1000 м 3 и более.
Наряду с радиографическим контролем может применяться рентгенотелевизионный контроль согласно установленным нормативным документам.
Радиографический контроль выполняется только после приемки сварных соединений по визуальному контролю.
При контроле пересечений швов рентгеновские пленки должны размещаться Т-образно или крестообразно - по две пленки на каждое пересечение швов.
Снимки должны иметь длину не менее 240 мм, а ширину - согласно соответствующим стандартам. Чувствительность снимков должна соответствовать 3-му классу согласно этому стандарту.
Маркировочные знаки должны устанавливаться согласно стандарту и содержать идентификационные номера резервуара и контролируемого конструктивного элемента, а также номер рентгенограммы, указанный на развертке контролируемого элемента.
Для соединений из деталей толщиной 8 мм и более допускается вместо радиографического контроля применять контроль ультразвуковой дефектоскопией.
7.5.2.2. Оценка внутренних дефектов сварных швов при радиографическом контроле должна производиться по соответствующим стандартам и должна соответствовать:
- для резервуаров III класса - 6-му классу;
- для резервуаров II класса - 5-му классу;
- для резервуаров I класса - 4-му классу.
Допускаемые виды и размеры дефектов в сварных соединениях в зависимости от их класса регламентируются соответствующими стандартами.
7.5.2.3. Радиографический контроль применяется для контроля стыковых сварных швов стенки и стыковых швов окраек днищ в зоне сопряжения со стенкой резервуаров.
Количество и размещение рентгенограмм устанавливается следующим образом: полотнища стенок резервуаров должны контролироваться в соответствии с табл. 7.3.;
Участки всех вертикальных сварных соединений в зонах примыкания к днищу длиной не менее 240 мм на резервуарах объему более 1000 м 3 подлежат обязательному контролю.
При выборе зон контроля вертикальных и горизонтальных соединений преимущественное внимание уделять проверке качества мест пересечения швов.
монтажные стыки полотнищ стенок должны контролироваться в объеме 100 % вертикальных швов и всех пересечений вертикальных и горизонтальных швов;
стенки резервуаров полистовой сборки должны контролироваться в соответствии с табл. 7.4;
8.1.1. Контроль качества сварных соединений при изготовлении и монтаже металлоконструкций резервуара осуществляется заказчиком, изготовителем и монтажной организацией.
8.1.2. Проектная организация осуществляет авторский надзор за сооружением резервуаров. Представителям заказчика, а также представителям проектной организации, выполняющим авторский надзор, предоставляются свободный доступ ко всем рабочим местам, где выполняются работы по изготовлению и монтажу металлоконструкций резервуара, и рабочая документация.
8.1.3. При сооружении резервуаров рекомендуется применять следующие методы контроля качества сварных соединений:
- механические испытания сварных соединений образцов-свидетелей;
- визуальный и измерительный контроль всех сварных соединений резервуара с применением шаблонов, линеек, отвесов, геодезических приборов и т.д.;
- контроль герметичности (непроницаемости) сварных швов с использованием проб "мел-керосин", ПВТ, избыточного давления воздуха или ПВК;
- физические методы - для выявления наличия внутренних дефектов: РК или УЗК, а для контроля наличия поверхностных дефектов с малым раскрытием - магнитопорошковым контролем или ПВК;
- гидравлические и пневматические прочностные испытания конструкции резервуара.
8.1.4. Методы контроля сварных соединений металлоконструкций резервуара представлены в таблице 27 настоящего Руководства по безопасности.
Таблица 27. Методы контроля сварных соединений металлоконструкций резервуара
Зона контроля | Метод контроля | |||||
---|---|---|---|---|---|---|
Визуальный и измери-тельный контроль | ПВТ | РК | УЗК | ПВК | Избыточным давлением | |
Днище | ||||||
Швы днища, швы накладок с днищем | + | + | - | - | - | - |
Швы днища на расстоянии 250 мм от наружной кромки | + | + | + | Допускается применение УЗК | - | - |
Стенка | ||||||
Вертикальные швы 1 и 2 поясов | + | - | + | Допускается применение УЗК | - | - |
Вертикальные швы остальных поясов | + | - | Допускается применение РК | + | - | - |
Горизонтальные швы поясов | + | - | Допускается применение РК | + | - | - |
Швы перекрестий вертикального и горизонтального шва | + | - | + | - | - | - |
Шов между патрубком и стенкой | + | + или проба ("мел-керосин") | - | + | - | - |
Шов между воротником патрубка (люка) и 1 поясом стенки | + | - | - | - | + | + |
Шов между воротником патрубка (люка) и стенкой (кроме 1 пояса) | + | - | - | - | - | + |
Радиальные швы колец жесткости | + | - | - | - | - | - |
Места удаления сборочных приспособлений, сварные соединения элементов конструкции после их термической обработки | + | - | - | - | + | - |
Шов стенки с днищем | + | + (с внутренней стороны) | - | - | + или проба "мел-керосин" (контроль пробой "мел-керосин" выполняется до сварки шва с внутренней стороны резервуара) | - |
Крыша | ||||||
Радиальные швы опорного кольца | + | - | - | + | - | - |
Швы настила кровли, щитов кровли | + | + | - | - | - | + |
Шов патрубка с кровлей | + | + | - | - | - | - |
Плавающая крыша (стальной понтон) | ||||||
Швы коробов (отсеков) и заглушек стоек | + | - | - | - | - | + (каждый короб, отсек) |
Швы центральной части | + | + | - | - | - | - |
Швы патрубков с крышей | + | + | - | - | - | - |
Примечания |
1. "+" - метод контроля применяется.
2. "-" - метод контроля не применяется.
3. При выборе зон контроля вертикальных и горизонтальных соединений преимущественное внимание следует уделять проверке качества мест пересечения швов.
8.2. Организация контроля
8.2.1. В проектной документации рекомендуется указывать методы и объемы контроля всех сварных соединений металлоконструкций резервуара, нормативы для оценки дефектности сварных швов и последовательность работ.
8.2.2. Ответственность за организацию контроля качества сварных соединений возлагается на руководителей сварочных работ от изготовителя и монтажника.
8.2.3. Контроль качества сварных соединений резервуаров физическими методами выполняется по заявке, в которой указываются характеристики соединения, тип и категория шва, толщина металла и марка стали, пространственное положение, объем контроля.
8.3. Визуальный и измерительный контроль
8.3.1. Визуальному и измерительному контролю подвергаются 100% длины всех сварных соединений резервуара.
8.3.2. Рекомендуемые требования к внешнему виду сварных швов:
- по форме и размерам соответствовать проектной документации;
- иметь гладкую или равномерно чешуйчатую поверхность (высота или глубина впадин не более 1 мм);
- металл шва иметь плавное сопряжение с основным металлом;
- отсутствие недопустимых внешних дефектов.
8.3.3. К недопустимым внешним дефектам сварных соединений металлоконструкций резервуара рекомендуется относить трещины любых видов и размеров, несплавления, наплывы, грубая чешуйчатость, наружные поры и цепочки пор, прожоги и свищи.
Подрезы основного металла рекомендуется выполнять не более величин, указанных в таблице 28 настоящего Руководства по безопасности.
8.3.4. Рекомендуемая выпуклость стыковых сварных швов в соответствии с таблицей 29 настоящего Руководства по безопасности.
Таблица 28. Допускаемая величина подреза
Сварное соединение | Класс резервуара по степени опасности | ||
---|---|---|---|
IV | III | I и II | |
Вертикальные поясные швы и соединение стенки с днищем | 5% толщины, но не более 0,5 мм | Не более 0,3 мм | Не более 0,2 мм |
Горизонтальные соединения стенки | 5% толщины, но не более 0,8 мм | 5% толщины, но не более 0,6 мм | 5% толщины, но не более 0,3 мм |
Прочие соединения | 5% толщины, но не более 0,8 мм | 5% толщины, но не более 0,6 мм | 5% толщины, но не более 0,6 мм |
Примечание. Длина подреза не более 10% длины шва. |
Таблица 29. Выпуклость стыковых сварных швов
Толщина листов, мм | Максимальная величина выпуклости, мм | |
---|---|---|
вертикальных соединений стенки | прочих соединений | |
До 12 | 1,5 | 2,0 |
Свыше 12 до 24 | 2,0 | 3,0 |
Свыше 24 | 3,0 | 3,0 |
8.3.5. Рекомендуемое смещение свариваемых кромок относительно друг друга для стыковых соединений из деталей одной толщины составляет:
- 1,0 мм - для деталей толщиной не более 10 мм;
- 10% толщины, но не более 3 мм - для деталей толщиной более 10 мм.
8.3.6. Рекомендуемая величина выпуклости или вогнутости углового шва не более чем на 20% величины катета шва.
8.3.7. Максимальные катеты угловых сварных швов рекомендуются не более 1,2 от толщины более тонкой детали в соединении.
Для деталей толщиной от 4 до 5 мм катет углового сварного шва рекомендуется брать равным 4 мм. Для деталей большей толщины катет углового шва определяется расчетом или конструктивно, но не менее 5 мм. Данное требование не распространяется на размер шва приварки настила легкосбрасываемой крыши к верхнему кольцевому элементу стенки.
Уменьшение катета углового шва рекомендуется не более 1 мм. Увеличение катета углового шва рекомендуется не более следующих значений:
- для катетов до 5 мм - 1,0 мм;
- для катетов свыше 5 мм - 2,0 мм.
8.3.8. В местах пересечения сварных швов и в местах исправления дефектов рекомендуется обеспечивать минимальную концентрацию напряжений за счет обеспечения плавного сопряжения шва с основным металлом.
8.4. Контроль герметичности
8.4.1. Контролю на герметичность рекомендуется подвергать все сварные швы, обеспечивающие герметичность резервуара, а также плавучесть и герметичность понтона или плавающей крыши.
8.4.2. Контроль герметичности сварных швов с использованием пробы "мел-керосин" рекомендуется производить путем обильного смачивания швов керосином. Нарушение герметичности сварного шва обнаруживается по появлению на противоположной стороне сварного шва пятен. Продолжительность контроля капиллярным методом зависит от толщины металла, типа сварного шва и температуры испытания. Заключение о наличии в сварном соединении сквозных дефектов оформляется не ранее чем через 1 ч после нанесения на шов индикатора сквозных дефектов.
8.4.3. При ПВТ вакуум-камеры создают разрежение над контролируемым участком с перепадом давления не менее 250 мм вод.ст. Перепад давления проверяются вакуумметром. Нарушение герметичности сварного шва обнаруживается по образованию пузырьков в нанесенном на сварное соединение мыльном или другом пенообразующем растворе.
8.4.4. Можно не производить контроль на герметичность стыковых соединений листов стенки толщиной 12 мм и более.
8.4.5. Контроль избыточным давлением применяется для проверки герметичности сварных швов приварки усиливающих листовых накладок люков и патрубков на стенке резервуаров. Контроль производится путем создания избыточного воздушного давления от 400 до 4000 мм вод.ст. в зазоре между стенкой резервуара и усиливающей накладкой с использованием для этого контрольного отверстия в усиливающей накладке. При этом на сварные швы внутри и снаружи резервуара наносится мыльная пленка, пленка льняного масла или другого пенообразующего вещества, позволяющего обнаружить утечки. После проведения испытаний контрольное отверстие заполняется ингибитором коррозии.
8.4.6. Контроль герметичности сварных соединений настила крыш резервуаров проводится в процессе гидравлических и пневматических испытаний за счет создания избыточного давления воздуха внутри резервуара до 150-200 мм вод.ст.
8.5. Физические методы контроля
8.5.1. Объем контроля сварных соединений резервуаров физическими методами рекомендуется определять в КМ в зависимости от:
- класса резервуара по степени опасности;
- категории сварного шва;
- уровня расчетных напряжений в сварном соединении;
- условий и режима эксплуатации резервуара, включая температуру эксплуатации, цикличность нагружения, сейсмичность района и т.д.
8.5.2. Радиографический контроль.
8.5.2.1. РК (рентгенографирование или гаммаграфирование) производится в соответствии с требованиями, установленными в проекте КМ.
Наряду с РК может применяться рентгенотелевизионный контроль согласно ГОСТ 27947-88 "Контроль неразрушающий. Рентгенотелевизионный метод. Общие требования", утвержденного постановлением Госстандарта СССР от 15 декабря 1988 года N 4155.
РК рекомендуется выполнять после приемки сварных соединений по визуальному и измерительному контролю.
При контроле пересечений швов рентгеновские пленки размещаются Т-образно или крестообразно по две пленки на каждое пересечение швов.
Снимки рекомендуется изготавливать длиной не менее 240 мм. Чувствительность снимков по 3 классу согласно ГОСТ 7512-82 "Контроль неразрушающий. Соединения сварные. Радиографический метод", утвержденного постановлением Госстандарта СССР от 20 декабря 1982 года N 4923.
Маркировочные знаки рекомендуются по ГОСТ 7512-82 "Контроль неразрушающий. Соединения сварные. Радиографический метод", утвержденному постановлением Госстандарта СССР от 20 декабря 1982 года N 4923, с содержанием идентификационных номеров резервуара и контролируемого конструктивного элемента, а также номера рентгенограммы, указанный на развертке контролируемого элемента.
Для соединений из деталей толщиной 6 мм и более вместо РК рекомендуется применять УЗК.
8.5.2.2. Рекомендуемый класс оценки внутренних дефектов сварных швов при РК:
- для резервуаров IV класса - 6 классу;
- для резервуаров III класса - 5 классу;
- для резервуаров I и II класса - 4 классу.
8.5.2.3. Рекомендуемые объемы физического контроля сварных швов (в %) стенок резервуаров в зависимости от класса опасности резервуаров указаны в таблице 30 настоящего Руководства по безопасности.
8.5.2.4. При обнаружении недопустимых дефектов сварного шва определяются границы дефектного участка. Кроме того, рекомендуется делать дополнительный снимок (не считая снимков, необходимых для определения границ дефекта) в любом месте этого же или другого шва, выполненного тем же сварщиком, который допустил дефект. На схемах расположения рентгенограмм указываются места, где были обнаружены недопустимые дефекты и проводилось исправления. Если в сварном соединении установлен уровень дефектности более 10%, то объем контроля таких швов удваивается.
Таблица 30. Объем контроля сварных соединений стенки резервуара физическими методами
Зона контроля | Класс опасности резервуара | ||||
---|---|---|---|---|---|
IV | III | II | I | ||
От 1000 до 9000 м 3 | От 10000 до 20000 м 3 | ||||
Вертикальные сварные соединения в поясах: | |||||
1, 2 | 20 | 25 | 50 | 100 | 100 |
3, 4 | 5 | 10 | 25 | 50 | 100 |
5, 6 | 2 | 5 | 10 | 25 | 50 |
остальные | - | - | 5 | 10 | 25 |
Горизонтальные сварные соединения между поясами: | |||||
1-2 | 3 | 5 | 10 | 15 | 20 |
2-3 | 1 | 2 | 5 | 5 | 10 |
3-4 | - | - | 2 | 2 | 5 |
остальные | - | - | - | 2 | 2 |
Примечания: |
1. При выборе зон контроля преимущество следует отдавать местам пересечения швов.
2. Монтажные стыки резервуаров рулонной сборки объемом от 1000 м 3 и более контролируются в объеме 100% длины швов.
8.5.3. Ультразвуковой контроль (УЗК).
8.5.3.1. УЗК проводится для выявления внутренних дефектов (трещин, непроваров, шлаковых включений, газовых пор) с указанием количества дефектов, их эквивалентной площади, условной протяженности и координат расположения.
8.5.3.2. УЗК проводится в соответствии с ГОСТ 14782-86 "Контроль неразрушающий. Соединения сварные. Методы ультразвуковые", утвержденным постановлением Госстандарта СССР от 17 декабря 1986 года N 3926.
8.5.4. Магнитопорошковой контроль или контроль проникающими веществами (ПВК).
Магнитопорошковый контроль или ПВК рекомендуется проводить в целях выявления поверхностных дефектов основного металла и сварных швов, не видимых невооруженным глазом. Магнитопорошковому контролю или ПВК подлежат:
- все вертикальные сварные швы стенки и швы соединения стенки с днищем резервуаров, эксплуатируемых при температуре хранимого продукта свыше 120°С;
- сварные швы приварки люков и патрубков к стенке резервуаров после их термической обработки;
- места на поверхности листов стенок резервуаров с пределом текучести свыше 345 МПа, где производилось удаление технологических приспособлений.
8.5.5. Контроль при гидравлических испытаниях резервуара.
8.5.5.1. При гидравлических испытаниях резервуара фиксируются и бракуются все места, где появляются течи и отпотины. После опорожнения резервуара в этих местах производятся ремонт и контроль.
8.5.5.2. Дефектные места в настиле стационарной крыши и в зоне ее примыкания к стенке, выявленные в процессе пневматических испытаний резервуара, фиксируются по появлению пузырьков на соединениях, покрытых пенообразующим раствором.
4.5.1. Организация-изготовитель (доизготовитель), монтажная или ремонтная организация обязаны применять такие виды и объемы контроля своей продукции, которые гарантировали бы выявление недопустимых дефектов, ее высокое качество и надежность в эксплуатации.
Контроль качества сварки и сварных соединений включает:
- проверку аттестации персонала;
- проверку сборочно-сварочного, термического и контрольного оборудования, аппаратуры, приборов и инструментов;
- контроль качества основных материалов;
- контроль качества сварочных материалов и материалов для дефектоскопии;
- операционный контроль технологии сварки;
- неразрушающий контроль качества сварных соединений;
- разрушающий контроль качества сварных соединений;
- контроль исправления дефектов.
Виды контроля определяются конструкторской организацией в соответствии с требованиями Правил, НД на изделия и сварку и указываются в конструкторской документации сосудов.
4.5.2. Для установления методов и объемов контроля сварных соединений необходимо определить группу сосуда в зависимости от расчетного давления, температуры стенки и характера среды по табл. 5.
Таблица 5
В тех случаях, когда в табл. 5 отсутствуют указанные сочетания параметров по давлению и температуре, для определения группы следует руководствоваться максимальным параметром.
Температура стенки определяется на основании теплотехнического расчета или результатов измерений, а при отсутствии этих данных принимается равной температуре среды, соприкасающейся со стенкой сосуда.
4.5.3. Объем контроля должен быть не менее предусмотренного Правилами.
4.5.4. В процессе изготовления сосудов должны проверяться:
- соответствие металла свариваемых деталей и сварочных материалов требованиям НД;
- соответствие качества подготовки кромок и сборки под сварку требованиям действующих стандартов и чертежей;
- соблюдение технологического процесса сварки и термической обработки, разработанных в соответствии с требованиями НД.
4.5.5. Основными видами неразрушающего контроля металла и сварных соединений являются:
- визуальный и измерительный;
- радиографический;
- ультразвуковой;
- радиоскопический (допускается применять только по инструкции, согласованной с Госгортехнадзором России);
- стилоскопирование;
- измерение твердости;
- гидравлические испытания;
- пневматические испытания.
Кроме этого могут применяться другие методы (акустическая эмиссия, магнитография, цветная дефектоскопия, определение содержания в металле шва ферритной фазы и др.) в соответствии с ТУ организации-изготовителя в объеме, предусмотренном НД.
4.5.6. При разрушающем контроле должны проводиться испытания механических свойств, металлографические исследования и испытания на стойкость против межкристаллитной коррозии.
4.5.7. Приемочный контроль изделия, сборочных единиц и сварных соединений должен выполняться после окончания всех технологических операций, связанных с термической обработкой, деформированием и наклепом металла.
Последовательность контроля отдельными методами должна соответствовать требованиям НД. Визуальный и измерительный контроль, а также стилоскопирование должны предшествовать контролю другими методами.
4.5.8. Контроль качества сварных соединений должен производиться по НД, согласованной в установленном порядке.
4.5.9. В процессе производства работ персоналом организации-производителя работ должен осуществляться операционный контроль технологических процессов подготовки и сборки деталей под сварку, сварки и термической обработки сварных соединений, исправления дефектов сварных соединений.
При операционном контроле проверяется соблюдение исполнителями требований настоящих Правил, НД и чертежей. Объемы операционного контроля при подготовке, сборке, сварке и термической обработке и исправлении дефектов должны указываться в НД.
4.5.10. Результаты по каждому виду контроля (в том числе и операционного) должны фиксироваться в отчетной документации (журналах, формулярах, протоколах, маршрутных паспортах и т.д.).
4.5.11. Средства контроля должны проходить метрологическую проверку.
4.5.12. Каждая партия материалов для дефектоскопии (пенетранты, порошок, суспензии, радиографическая пленка, химические реактивы и т.д.) до начала их использования должна быть подвергнута входному контролю.
4.5.13. Объем разрушающего и неразрушающего контроля, предусмотренный Правилами, может быть уменьшен по согласованию с Госгортехнадзором России в случае массового изготовления, в том числе при неизменном технологическом процессе, специализации сварщиков на отдельных видах работ и высоком их качестве, подтвержденном результатами контроля за период не менее 6 месяцев. Копия разрешения вкладывается в паспорт сосуда.
4.5.14. Методы и объемы контроля сварных соединений приварных деталей, не работающих под внутренним давлением, должны устанавливаться НД на изделие и сварку.
4.5.15. Изделие признается годным, если при контроле в нем не будут обнаружены внутренние и наружные дефекты, выходящие за пределы допустимых норм, установленных Правилами и НД на изделие и сварку.
4.5.16. Сведения о контроле сварных соединений основных элементов сосудов, работающих под давлением, должны заноситься в паспорт сосуда.
4.5.17. Визуальному и измерительному контролю подлежат все сварные соединения сосудов и их элементов в целях выявления в них следующих дефектов:
- трещин всех видов и направлений;
- свищей и пористости наружной поверхности шва;
- подрезов;
- наплывов, прожогов, незаплавленных кратеров;
- смещения и совместного увода кромок свариваемых элементов свыше норм, предусмотренных Правилами;
- непрямолинейность соединяемых элементов;
- несоответствие формы и размеров швов требованиям технической документации.
4.5.18. Перед визуальным осмотром поверхность сварного шва и прилегающие к нему участки основного металла шириной не менее 20 мм в обе стороны от шва должны быть зачищены от шлака и других загрязнений, при электрошлаковой сварке это расстояние должно быть не менее 100 мм.
4.5.19. Осмотр и измерения сварных соединений должны производиться с наружной и внутренней сторон по всей протяженности швов. В случае невозможности осмотра и измерения сварного соединения с двух сторон его контроль должен производиться в порядке, предусмотренном автором проекта.
4.5.20. Ультразвуковая дефектоскопия и радиографический контроль производятся в целях выявления в сварных соединениях внутренних дефектов (трещин, непроваров, пор, шлаковых включений и др.).
4.5.22. Ультразвуковая дефектоскопия и радиографический контроль сварных соединений должны производиться в соответствии с требованиями НД.
4.5.23. Метод контроля (ультразвуковая дефектоскопия, радиографический контроль, оба метода в сочетании) выбирается исходя из возможности обеспечения более полного и точного выявления недопустимых дефектов с учетом особенностей физических свойств металла, а также освоенности данного метода контроля для конкретного вида сварных соединений.
4.5.24. Объем контроля ультразвуковой дефектоскопией или радиографическим методом стыковых, угловых, тавровых и других сварных соединений сосудов и их элементов (днищ, обечаек, штуцеров, люков, фланцев и др.), включая соединения люков и штуцеров с корпусом сосуда, должен соответствовать указанному в табл. 6.
Таблица 6
Указанный объем контроля относится к каждому сварному соединению. Места сопряжений (пересечений) сварных соединений подлежат обязательному контролю ультразвуковой дефектоскопией или радиографическим методом.
Ультразвуковая дефектоскопия или радиографический контроль швов приварки внутренних и наружных устройств к корпусу сосуда должны производиться при наличии требования в технической документации.
4.5.25. Сварные соединения сосудов, снабженных быстросъемными крышками, подлежат контролю ультразвуковой дефектоскопией или радиографическим методом в объеме 100 %.
4.5.26. Для сосудов 3-й и 4-й групп места радиографического или ультразвукового контроля устанавливаются отделом технического контроля организации-изготовителя после окончания сварочных работ по результатам внешнего осмотра.
4.5.27. Перед контролем соответствующего участка сварные соединения должны быть так замаркированы, чтобы их можно было легко обнаружить на картах контроля и радиографических снимках.
4.5.28. При выявлении недопустимых дефектов в сварных соединениях, подвергаемых ультразвуковой дефектоскопии или контролю радиографическим методом в объеме менее 100 %, обязательному контролю тем же методом подлежат однотипные швы этого изделия, выполненные данным сварщиком, по всей длине соединения.
4.5.29. При невозможности осуществления ультразвуковой дефектоскопии или радиографического контроля из-за недоступности отдельных сварных соединений или при неэффективности этих методов контроля (в частности, швов приварки штуцеров и труб внутренним диаметром менее 100 мм) контроль качества этих сварных соединений должен производиться другими методами в соответствии с инструкцией, согласованной в установленном порядке. Указания об использованном методе контроля заносятся в паспорт сосуда.
4.5.30. Ультразвуковая дефектоскопия и радиографический контроль стыковых сварных соединений по согласованию с Госгортехнадзором России могут быть заменены другим эффективным методом неразрушающего контроля.
4.5.31. Капиллярный и магнитопорошковый контроль сварных соединений и изделий являются дополнительными методами контроля, устанавливаемыми чертежами и НД в целях определения поверхностных или подповерхностных дефектов.
4.5.32. Капиллярный контроль должен производиться в соответствии с методиками контроля, согласованными в установленном порядке.
4.5.33. Класс и уровень чувствительности капиллярного и магнитопорошкового контроля должны устанавливаться чертежами и НД.
4.5.34. Контроль стилоскопированием должен проводиться в целях подтверждения соответствия легирования металла деталей и сварных швов требованиям чертежей и НД.
4.5.35. Стилоскопированию подвергаются:
- все свариваемые детали (части конструкций), которые по чертежу должны изготавливаться из легированной стали;
- металл шва всех сварных соединений труб, которые согласно НД должны выполняться легированным присадочным материалом;
- сварочные материалы согласно ст. 4.3.10 Правил.
4.5.36. Стилоскопирование должно проводиться в соответствии с требованиями методических указаний или инструкций, согласованных в установленном порядке.
4.5.37. Измерение твердости металла шва сварного соединения проводится в целях проверки качества выполнения термической обработки сварных соединений.
4.5.38. Измерению твердости подлежит металл шва сварных соединений, выполненных из легированных теплоустойчивых сталей перлитного и мартенситно-ферритного классов методом и в объеме, установленными НД.
4.5.39. Контроль механических свойств, испытание на стойкость против межкристаллитной коррозии и металлографические исследования сварных соединений должны производиться на образцах, изготовленных из контрольных сварных соединений.
Контрольные сварные соединения должны воспроизводить одно из стыковых сварных соединений сосуда, определяющих его прочность (продольные швы обечаек, хордовые и меридиональные швы выпуклых днищ), а также кольцевые швы сосудов, не имеющих продольных швов.
Контрольные сварные соединения должны быть идентичны контролируемым производственным сварным соединениям (по маркам стали, толщине листа или размерам труб, форме разделки кромок, методу сварки, сварочным материалам, положению шва, режимам и температуре подогрева, термообработке) и выполнены тем же сварщиком и на том же сварочном оборудовании одновременно с контролируемым производственным соединением. Контрольные сварные соединения для кольцевых швов многослойных сосудов устанавливаются НД на изготовление этих сосудов.
Если проведена производственная аттестация технологии сварки в соответствии с требованиями Правил, то по согласованию со специализированными организациями разрешается не выполнять механические испытания контрольных сварных соединений.
4.5.40. При сварке контрольных соединений (пластин), предназначенных для проверки механических свойств, проведения испытания на стойкость против межкристаллитной коррозии и металлографического исследования, пластины следует прихватывать к свариваемым элементам так, чтобы шов контрольных пластин являлся продолжением шва свариваемого изделия.
Сварка контрольных пластин для проверки соединений элементов сосудов, к которым прихватка пластин невозможна, может производиться отдельно от них, но с обязательным соблюдением всех условий сварки контролируемых стыковых соединений.
4.5.41. При автоматической (механизированной) сварке сосудов на каждый сосуд должно быть сварено одно контрольное соединение. Если в течение рабочей смены по одному технологическому процессу сваривается несколько однотипных сосудов, разрешается на всю партию сосудов, сваренных в данной смене, выполнить одно контрольное соединение. При ручной сварке сосудов несколькими сварщиками каждый из них должен сварить по одному контрольному соединению на каждый сосуд.
4.5.42. При серийном изготовлении сосудов в случае 100 % контроля стыковых сварных соединений ультразвуковой дефектоскопией или радиационным методом допускается на каждый вид сварки варить по одному контрольному соединению на всю партию сосудов. При этом в одну партию могут быть объединены сосуды, аналогичные по назначению и типу, изготовляемые из одного вида металлопродукции (листа, трубы, поковки и т.п.), одной марки металла, имеющие одинаковую форму разделки кромок, выполненные по единому технологическому процессу и подлежащие термообработке по одному режиму, если цикл изготовления всех изделий по сборочно-сварочным работам, термообработке и контрольным операциям не превышает трех месяцев.
4.5.43. При контроле качества сварных соединений в трубчатых элементах со стыковыми швами одновременно со сваркой последних должны изготовляться в тех же производственных условиях контрольные стыки для проведения испытаний механических свойств соединений. Число контрольных стыков должно составлять 1 % общего числа сваренных каждым сварщиком однотипных стыков, но не менее одного стыка на каждого сварщика.
4.5.44. Сварка контрольных соединений во всех случаях должна осуществляться сварщиками, выполнявшими контролируемые сварные соединения на сосудах.
4.5.45. Размеры контрольных соединений должны быть достаточными для вырезки из них необходимого числа образцов всех предусмотренных видов механических испытаний, испытания на стойкость против межкристаллитной коррозии, металлографического исследования, а также для повторных испытаний.
4.5.46. Контрольные сварные соединения должны подвергаться ультразвуковой дефектоскопии или радиационному контролю по всей длине.
Если в контрольном соединении будут обнаружены недопустимые дефекты, все производственные сварные соединения, представленные данным соединением и не подвергнутые ранее дефектоскопии, подлежат проверке неразрушающим методом контроля по всей длине.
4.5.47. Механическим испытаниям должны подвергаться контрольные стыковые сварные соединения в целях проверки соответствия их механических свойств требованиям Правил и технических условий на изготовление сосуда.
Обязательные виды механических испытаний:
- на статическое растяжение - для сосудов всех групп (см. табл. 5);
- на статический изгиб или сплющивание - для сосудов всех групп;
- на ударный изгиб - для сосудов, предназначенных для работы при давлении более 5 МПа (50 кгс/см 2 ) или температуре выше 450 °С, и сосудов, изготовленных из сталей, склонных к подкалке при сварке (приложение 4);
- на ударный изгиб - для сосудов 1, 2, 3-й групп, предназначенных для работы при температуре ниже -20 °С.
Испытания на ударный изгиб сварных соединений производятся для сосудов и их элементов с толщиной стенки 12 мм и более по п. 3 при температуре 20 °С, а по п. 4 - при рабочей температуре.
Если проведена производственная аттестация технологии сварки в соответствии с требованиями Правил, то по согласованию со специализированными организациями разрешается не выполнять механические испытания контрольных сварных соединений.
4.5.48. Из каждого контрольного стыкового сварного соединения должны быть вырезаны:
- два образца для испытания на статическое растяжение;
- два образца для испытаний на статический изгиб или сплющивание;
- три образца для испытания на ударный изгиб.
4.5.49. Испытания на статический изгиб контрольных стыков трубчатых элементов сосудов с условным проходом труб менее 100 мм и толщине стенки менее 12 мм могут быть заменены испытанием на сплющивание.
4.5.50. Механические испытания сварных соединений должны выполняться в соответствии с требованиями государственных стандартов.
4.5.51. Временное сопротивление разрыву металла сварных швов при температуре 20 °С должно соответствовать значениям, установленным в НД на основной металл. Допускается снижение временного сопротивления разрыву, если это предусмотрено нормативной документацией, согласованной в установленном порядке.
4.5.52. При испытании стальных соединений на статический изгиб полученные показатели должны быть не ниже показателей, приведенных в табл. 7.
4.5.1. Организация - изготовитель (доизготовитель), монтажная или ремонтная организация обязаны применять такие виды и объемы контроля своей продукции, которые гарантировали бы выявление недопустимых дефектов, ее высокое качество и надежность в эксплуатации.
Контроль качества сварки и сварных соединений включает:
проверку аттестации персонала;
проверку сборочно - сварочного, термического и контрольного оборудования, аппаратуры, приборов и инструментов;
контроль качества основных материалов;
контроль качества сварочных материалов и материалов для дефектоскопии;
операционный контроль технологии сварки;
неразрушающий контроль качества сварных соединений;
разрушающий контроль качества сварных соединений;
контроль исправления дефектов.
Виды контроля определяются конструкторской организацией в соответствии с требованиями настоящих Правил, НД на изделия и сварку и указываются в конструкторской документации сосудов.
4.5.2. Для установления методов и объемов контроля сварных соединений необходимо определить группу сосуда в зависимости от расчетного давления, температуры стенки и характера среды по табл. 5.
(в ред. Постановления Госгортехнадзора РФ от 02.09.97 N 25)
Группа сосудов | Расчетное давление, МПа (кгс/кв. см) | Температура стенки, град. C | Рабочая среда |
1 | свыше 0,07 (0,7) | независимо | взрывоопасная или пожароопасная, или 1-го, 2-го классов опасности по ГОСТ 12.1.007 |
2 | до 2,5 (25) | ниже -70, выше 400 | |
свыше 2,5 (25) до 4 (40) | ниже -70, выше 200 | ||
свыше 4 (40) до 5 (50) | ниже -40, выше 200 | ||
свыше 5 (50) | независимо | любая, за исключением указанной | |
3 | до 1,6 (16) | от -70 до -20 | для 1-й группы |
от 200 до 400 | сосудов | ||
свыше 1,6 (16) до 2,5 (25) | от -70 до 400 | ||
свыше 2,5 (25) до 4 (40) | от -70 до 200 | ||
свыше 4 (40) до 5 (50) | от -40 до 200 | ||
4 | до 1,6 (16) | от -20 до 200 |
В тех случаях, когда в табл. 5 отсутствуют указанные сочетания параметров по давлению и температуре, для определения группы следует руководствоваться максимальным параметром.
Температура стенки определяется на основании теплотехнического расчета или результатов измерений, а при отсутствии этих данных принимается равной температуре среды, соприкасающейся со стенкой сосуда.
4.5.3. Объем контроля должен быть не менее предусмотренного настоящими Правилами.
4.5.4. В процессе изготовления сосудов должны проверяться:
соответствие металла свариваемых деталей и сварочных материалов требованиям НД;
соответствие качества подготовки кромок и сборки под сварку требованиям действующих стандартов и чертежей;
соблюдение технологического процесса сварки и термической обработки, разработанных в соответствии с требованиями НД.
4.5.5. Основными видами неразрушающего контроля металла и сварных соединений являются:
визуальный и измерительный;
радиоскопический (допускается применять только по инструкции, согласованной с Госгортехнадзором России);
Кроме этого могут применяться другие методы (акустическая эмиссия, магнитография, цветная дефектоскопия, определение содержания в металле шва ферритной фазы и др.) в соответствии с ТУ организации - изготовителя в объеме, предусмотренном НД.
Контроль материалов и сварных соединений неразрушающими методами должен проводиться организациями, имеющими разрешение (лицензию) органов Госгортехнадзора России на выполнение этих работ.
4.5.6. При разрушающем контроле должны проводиться испытания механических свойств, металлографические исследования и испытания на стойкость против межкристаллитной коррозии.
4.5.7. Приемочный контроль изделия, сборочных единиц и сварных соединений должен выполняться после окончания всех технологических операций, связанных с термической обработкой, деформированием и наклепом металла.
Последовательность контроля отдельными методами должна соответствовать требованиям НД. Визуальный и измерительный контроль, а также стилоскопирование должны предшествовать контролю другими методами.
4.5.8. Контроль качества сварных соединений должен производиться по НД, согласованной с Госгортехнадзором России.
4.5.9. В процессе производства работ персоналом организации - производителя работ должен осуществляться операционный контроль технологических процессов подготовки и сборки деталей под сварку, сварки и термической обработки сварных соединений, исправления дефектов сварных соединений.
При операционном контроле проверяется соблюдение исполнителями требований настоящих Правил, НД и чертежей. Объемы операционного контроля при подготовке, сборке, сварке и термической обработке и исправлении дефектов должны указываться в НД.
4.5.10. Результаты по каждому виду контроля (в том числе и операционного) должны фиксироваться в отчетной документации (журналах, формулярах, протоколах, маршрутных паспортах и т.д.).
4.5.11. Средства контроля должны проходить метрологическую проверку в соответствии с требованиями нормативной документации Госстандарта России.
4.5.12. Каждая партия материалов для дефектоскопии (пенетранты, порошок, суспензии, радиографическая пленка, химические реактивы и т.д.) до начала их использования должна быть подвергнута входному контролю.
4.5.13. Объем разрушающего и неразрушающего контроля, предусмотренный настоящими Правилами, может быть уменьшен по согласованию с Госгортехнадзором России в случае массового изготовления, в том числе при неизменном технологическом процессе, специализации сварщиков на отдельных видах работ и высоком их качестве, подтвержденном результатами контроля за период не менее 6 месяцев. Копия разрешения вкладывается в паспорт сосуда.
4.5.14. Методы и объемы контроля сварных соединений приварных деталей, не работающих под внутренним давлением, должны устанавливаться НД на изделие и сварку.
4.5.15. Изделие признается годным, если при контроле в нем не будут обнаружены внутренние и наружные дефекты, выходящие за пределы допустимых норм, установленных настоящими Правилами и НД на изделие и сварку.
4.5.16. Сведения о контроле сварных соединений основных элементов сосудов, работающих под давлением, должны заноситься в паспорт сосуда.
1980 год. Северное море, Норвегия. Разлом буровой платформы.
2004 год. CША, Хьюстон. Взрыв и сильный пожар на нефтехимическом заводе.
2016 год. Канада. Разлив 63,6 тыс. литров нефти из-за утечки в нефтепроводе.
Причиной всех этих аварий стала некачественная сварка. Там не доглядели, там упустили, там понадеялись на авось. Жертвы, разрушения, убытки.
Предотвратить подобные инциденты призван своевременный и профессиональный контроль качества сварных швов и соединений.
Кто уполномочен проводить контроль качества сварных швов и соединений?
Контроль осуществляет аттестованный специалист. В РФ аттестацию специалистов сварочных технологий проводит Национальное Агентство Контроля Сварки (НАКС), которое ведет соответствующий реестр аттестованного персонала. Кроме того, для целей контроля качества сварных швов необходимо пройти аттестацию по неразрушающему контролю.
Аттестации в НАКС подлежат также оборудование, приборы и инструменты, применяемые при контроле. Сертификаты выдаются сроком на один год. Без этого пакета документов использование сварочного оборудования и приборов для контроля качества сварки запрещено.
Что подлежит контролю?
Сварка бывает ручная, полуавтоматическая и автоматическая.
- Ручная сварка - это процесс создания соединения при помощи электрической дуги. Дуга между поверхностью металла и электродом зажигается и стабильно горит, формируя практически ровный шов. В работе применяются электроды не длиннее 45 см.
- Полуавтоматическая - сварочный процесс, при котором электрод подается в зону сварки с переменной или постоянной скоростью, куда одновременно поступает инертный или активный газ. Это могут быть и смеси, которые защищают нагретые элементы от воздействия окружающей среды. Такая сварка обеспечивает высококачественный шов и удобство работы.
- Автоматическая - это механизированный вид сварки. Направление и скорость движения электрода выполняется автоматическим способом. Для данного метода требуются ровные поверхности свариваемых элементов.
Как правило, к контролю предъявляется ручная сварка. При ручной сварке в металле и сварных швах часто образуются дефекты, которые влияют на качество изделия. Серьезные изъяны могут привести к непоправимым последствиям - разрыву трубопровода, разрушению металлоконструкций или обрушению из-за некачественно сваренной арматуры.
Где и когда проводится контроль сварных швов и соединений?
Для проведения проверки инспектор выезжает
- на место производства сварочных работ при изготовлении изделия,
- на объект, где сварные изделия будут свариваться между собой, монтироваться и применяться.
Рассмотрим в качестве примера трубы.
Наибольшего эффекта можно добиться, используя комбинацию этих инспекций, то есть проводя как контроль производства трубной продукции, так и её входной контроль на объекте.
О методах и порядке проведения контроля сварных швов читайте в нашей следующей статье.
Группа SGS является мировым лидером на рынке контроля, экспертизы, испытаний и сертификации. Основанная в 1878 году, сегодня SGS признана эталоном качества и деловой этики. Более 94,000 сотрудников работает в сети SGS, насчитывающей свыше 2,600 офисов и лабораторий по всему миру со штаб-квартирой в Женеве, Швейцария.
Автор статьи
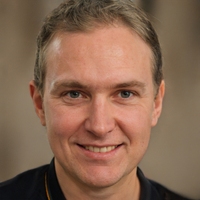
Читайте также: