Какие трубы применяют на судах на подводных крыльях стальные
Обновлено: 25.04.2024
В судовых системах современных морских судов применяют стальные, стальные оцинкованные, медные, латунные алюминиевые, титановые и пластмассовые трубы. Трубопроводы выполняют из отдельных труб, соединенных между собой разъемными (фланцевыми, штуцерными, муфтовыми и др.) и неразъемными (сварными, паяными) соединениями. В трубопроводах морской и пресной воды применяются трубы: стальные оцинкованные и со стеклоэмалевым покрытием, медные и полиэтиленовые. Для трубопроводов водяного пара используют стальные и медные трубы, а для сжатого воздуха — легированные стальные или биметаллические (футерованные изнутри слоем меди). Вентиляционные воздуховоды изготовляют из стальных или алюминиево-магниевых труб круглого и прямоугольного сечения больших размеров.
ГОСТами и ОСТами нормализованы химические, физические, геометрические и условные характеристики труб. Химические характеристики определяют качественный состав материала, из которого изготовлены трубы. Физические характеристики определяют механические и технологические качества материала труб. К ним относятся параметры — предел текучести σТ, предел временного сопротивления σв, относительное удлинение б, ударная вязкость а — и различные технологические пробы (на изгиб, отбортовку, сплющивание и др.).
Геометрические характеристики определяют размеры и форму труб. К ним относятся наружный диаметр DB, толщина стенки s, длина однородной части труб l.
В подлежащих надзору Регистра СССР трубопроводах с внутренним давлением металлических труб толщина стенки, мм, должна быть не менее s = s0 + b + с, где s0 = Dнp/ (200σдφ + р); р — расчетное давление, являющееся максимальным рраб, которое должно приниматься равным наибольшему давлению открытия предохранительных клапанов, МПа; b — 0,4Dнs/R — прибавка к толщине, учитывающая фактическое утонение стенки трубы при гибке, мм; с — прибавка на коррозию трубы, мм; φ — коэффициент прочности продольного сварного шва; R — средний радиус гиба трубы, мм.
Полученную расчетным путем толщину стенки нужно округлить до ближайшего большего значения, предусмотренного соответствующим стандартом на трубы.
После изготовления трубы испытываются на прочность пробным гидравлическим давлением (1,25÷2) ру. Смонтированные на судне трубопроводы подвергаются гидравлическому испытанию на плотность соединений давлением (1,25÷1,5) рраб.
Как это возможно — уложить сотни километров стальных труб на огромную глубину, на дно со сложным рельефом? Как добиться, чтобы вся эта конструкция выдерживала огромное давление, не смещалась, не была уничтожена коррозией, выдерживала удары корабельных якорей и рыболовного снаряжения и, наконец, просто работала как надо? Самым свежим примером сооружения подводного мегатрубопровода стал знаменитый «Северный поток», пролегший по балтийскому дну и соединивший российскую и немецкую газотранспортные системы. Две нитки труб, каждая длиной более 1200 км — почти 2,5 млн тонн стали, поглощенных морем по воле человека. Именно на примере «Северного потока» мы попытаемся вкратце рассказать о технологиях создания подводных трубопроводов.
Две нитки газопровода состоят из 199 755 двенадцатиметровых труб, сделанных из высокосортной углеродистой стали. Но коль скоро речь идет о соприкосновении с такой химически агрессивной средой, как морская вода, металлу нужна защита. Для начала на внешнюю поверхность трубы наносят трехслойное покрытие из эпоксидного состава и полиэтилена — это делается прямо на заводе-производителе.
Можно ли укладывать такую трубу на морское дно? Нет, ее требуется дополнительно защищать и усиливать против давления воды и электрохимических процессов. На трубы устанавливают так называемую катодную защиту (наложение отрицательного потенциала на защищаемую поверхность). С определенным шагом к трубам приваривают электроды, соединенные между собой анодным кабелем, который связан с источником постоянного тока. Но главное, что еще предстоит сделать с трубой, прежде чем она будет готова опуститься на дно, — это обетонирование. На специальных заводах внешнюю поверхность трубы покрывают слоем бетона толщиной 60−110 мм. После обетонирования труба приобретает вес около 24 т. У нее появляется серьезная защита против механических воздействий, а дополнительная масса позволяет ей стабильно лежать на дне.
Но надо помнить, что дно даже такого сравнительно неглубокого моря, как Балтийское, не предоставит само по себе удобного и безопасного ложа для газопровода. Есть два фактора, которые неизбежно приходилось учитывать проектировщикам и строителям «Северного потока»: антропогенный и природный.
История судоходства в североевропейском регионе насчитывает тысячелетия, и потому на дне моря скопилось немало всевозможного мусора, а также обломков затонувших кораблей. XX век внес свой страшный вклад: на Балтике в ходе мировых войн велись активные боевые действия, устанавливались сотни тысяч морских мин, а по окончании войн в море же утилизировались боеприпасы, в том числе и химические. Для мониторинга боеприпасов применялись корабли, оснащенные эхолокационным оборудованием, а также специальным донным роботом (ROV), связанным кабелем с базовой донной станцией TMS.
Другой фактор, природный, связан c особенностями рельефа дна. Дно моря сложено из различных пород, оно имеет выступающие гребни, впадины, расселины, и опускать трубы прямо на все это геологическое разнообразие не всегда возможно. Если допустить большое провисание нитки газопровода между двумя естественными опорами, конструкция может со временем разрушиться со всеми вытекающими из этого неприятностями. Поэтому донный рельеф для прокладки необходимо искусственным образом исправлять.
Теперь, пожалуй, самое интересное: как трубы оказываются на дне? Разумеется, сложно себе представить, что каждая отдельная 12-метровая труба приваривается к нитке газопровода прямо в море на глубине. Значит, эту процедуру необходимо проделывать до укладки. Что, собственно, и происходит на борту трубоукладочного судна. Тут необходимо ненадолго вернуться к конструкции самой трубы и заметить, что после нанесения на нее антикоррозионной защиты и утяжеляющего бетонирования оконцовки труб остаются открытыми и незащищенными, — иначе сварка была бы затруднена. Поэтому участки соединений защищаются от коррозии уже после сварки.
Далее происходит укладка S-образным способом. Сваренная из труб плеть приобретает в процессе укладки форму, напоминающую латинскую букву S. Плеть под небольшим углом выходит из кормы корабля, достаточно резко опускается вниз и достигает дна, где принимает горизонтальное положение. Труднее всего представить себе, что нить из стальных, покрытых бетоном 24-тонных труб способна к таким резким изгибам без разрушения, однако все происходит именно так.
Прежде чем использовать газопровод для перекачки топлива, его испытывали… водой. Внутрь секций с помощью поршневого модуля была закачана предварительно отфильтрованная от взвесей и даже бактерий морская вода. Жидкость, нагнетавшаяся со специального судна, создавала внутри плети давление, превышающее рабочее, и такой режим поддерживался в течение суток. Затем вода откачивалась, и секция газопровода осушалась. Еще до того, как в трубопроводе появился природный газ, его трубы заполнялись азотом.
Прокладка газопровода по морскому дну — лишь часть проекта «Северный поток». Немало усилий и затрат потребовалось для оборудования береговой инфраструктуры. Отдельная история — это вытягивание нитки газопровода на берег с помощью мощной лебедки или создание механизма компенсации сезонного сжатия-расширения 1200-километровой нитки.
Строительство «Северного потока» вызвало немало дискуссий на разные околополитические темы — от экологии до чрезмерной роли сырьевого экспорта в экономике России. Но если абстрагироваться от политики, нельзя не заметить: трансбалтийский газопровод — отличный пример того, как продвинутые технологии и международная кооперация способны творить современные чудеса во вполне рабочем рутинном режиме.
Статья «Подводные нити» опубликована в журнале «Популярная механика» (№8, Август 2013).
Покрытие трубы мало того что трёхслойное ,оно ещё и с крошкой выполняется для улучшения адгезии с бетоном. Ну и труба под газ идёт с внутренним покрытием.Для уменьшения сопротивления . Нефтянка в этом плане проще, по понятным причинам,да и стенка у нефтяной трубы существенно тоньше.
Про вес - интересный момент. Я не помню к сожалению диаметр трубы которая шла на Северный ,но 24 тонны это минимум в 2 раза тяжелее. Следовательно -от 12 тонн бетона на трубу.Это интересный момент.
Спасибо большое за пост, а то начал терять веру в позновательность пикабу.
Колосально! Древние римляне с их акведуками обзавидовались бы)
Кто таким постам минусы ставит?
В свое время поработал на Кашаганском месторождении. На северном Каспии глубина не большая, поэтом трубы клали на специальные плоты отрезками, потом топили, а позже доставали концы и варили.
Как поддерживается давление на всей протяжённости трассы? Насосы под водой на трубе сидят?
Учите, дети, сопромат!
А можно поменьше пафоса? Продвинутые технологии, современные чудеса.
Защищать подводные конструкции от морской воды начали даавно.
Трансатлантический кабель проложили 150 лет назад. С поддержанием давления в бетонированной трубе проблем нет (хотя не факт, что её раздавит, 200 м всего), но расстояние, глубина, рельеф, условия работы, технологический уровень делают задачу горааздо сложнее.
А что, уже придумали не-углеродистую сталь?
На трубы устанавливают так называемую катодную защиту (наложение отрицательного потенциала на защищаемую поверхность). С определенным шагом к трубам приваривают электроды, соединенные между собой анодным кабелем
Вы уж там определитесь: анодная или катодная защита? Если кабель - анод, то почему защита "катодная"?
И сколько мощности, интересно, эта защита требует?
Атак интересно, конечно: сколько русских денег вбухано в эту трубу и всё для того, чтобы немцы русский газ подешевле получали. Что, в России всё уже газифицировано? Не, в мире розовых пони всем на этот вопрос наплевать, там всё общее и всё - бесплатно. А мы уже дважды с Германией воевали в Мировых войнах, нам-то нахрена её усиливать снова?
Ну, и не о политике.
Интересно, эти сварные стыки тоже бетонируют, прямо на корабле? И долго этот бетон схватывается? Когда это делают на заводе, там особо спешить некуда, а вот на судне-укладчике времени не так уж много.
мда, а как потом диагностировать будут 1200 км? наружкой по дну бегать?
Вот и я встретил ту, кого надо добиваться
Собственно заголовок говорит за себя. Познакомились в тиндере (т9 сначала исправил на тандыр). Художник она. Общались. Что понравилось - писала сама, спрашивала всякую мелочь, интересовалась в общем. Общение перешло в телеграмм. Обменивались фотками, дикпиков с моей стороны не было, с её тоже, что хорошо, я приверженец старой школы. В общем - прошла неделя плотного такого общения. Виртуального. Решили встретиться.
Встречу назначили в центре города. Встретились. Погуляли. Неловкого молчания не было, я сыпал остротами и шутил, она смеялась. Немного раздражал её смех, похожий на скрип пружин старого дивана, но кто не без греха. Потом я перестал обращать на это внимание. Взяли по кофе.
Первый звоночек прозвенел когда она начала говорить про энергию. Про энергетическую совместимость людей. Рассказала что ходила на массаж, но отказала массажисту. Да, отказала в том, что бы он сделал ей массаж. На мой закономерный вопрос о внешности сказала что он был симпатичный и стройный. Просто не тянуло к нему. Не сошлись ауры. А я вот её притягиваю. Есть, мол, контакт у нас. Собственно говоря, меня это радовало - контакта хотелось: дамой она была симпатичной и, не смотря на двоих детей, стройной и с нужными выпуклостями в нужных местах. Классным завершением это вечера стал блюз-концерт на одной из молодёжных площадок.
Так мы общались ещё три дня и решили опять погулять. Я ей привёз клубнику с огорода. Ей вроде как это понравилось. Мы опять говорили друг о друге. Все было классно, вот правда. Идём. И тут она просто замолчала. Спрашиваю: почему у нас монолог, а не диалог. И тут ещё один звонок. Точнее маленький гром. "У меня настроение пропало. Я домой хочу". Вызови, говорит, мне такси, не хочу гулять. Оки. Вызвал. Ладно, думаю, посмотрим.
Вечером, в переписке, на мой вопрос о том, мол, что это было, мне пришёл ответ что я должен был её остановить, уговорить остаться и вообще включить мужика. Ладно, думаю, глянем.
Решили встретиться ещё раз. Она была инициатором - соскучиласьвседела. Приятно конечно было слышать, но такой уставший с работы был, что хотелось только принять душ и завалиться на диван, предварительно полив огород конечно, ибо стояла жара +30. В общем решил приехать. Вызвал такси, ибо автобус уже не ходит. В одну сторону от меня в это время в центр города выходит 500-600р, что для нашего города не сказать что мало. Приехал к её дому. Написал что я на месте, жду только её. Купил ведёрко мороженого, думал прикольно будет его идти и кушать, романтика ж. Ложки естественно тоже купил. Целый набор, блин, ибо поштучно не продавались. Фигня. Жду. Пишу. Вижу что читает, не не отвечает. Чувствую что пахнет гавной, но жду. Начал есть мороженое. А, я звонил ей раза три, она не брала трубку. Прошло минут двадцать, ведёрко ополовинилось. Звонит. И я просто обалдел. Привет, говорит, как дела, я малину кушала, вкусная такая. Я: дамочка, вы ничего не забыли? Я так-то тут. Занята была она! Выбирала малину, она её очень любит. Честно говоря, я такое первый раз видел. Обиделся, спрашивает. Нет, говорю, все ништяк, подумаешь, приехал из своих ебеней в центр, после работы, реально уставший, все нормально. Сарказмом в моем голосе можно было пробить броник сапера, но, видимо, её броня была как у танка. Аааа, ну ладно, говорит, хорошо добраться до дома, пока.
В полном ахтунге от такого я приехал домой. Не писал ей дня два, ибо нахер мне это надо. Тут позвал сосед на плов на огне. Стоим, пьём пиво, смотрим на его детей плещущихся в бассейне, идиллия. И тут пишет она. Приветиккакделачтонепишешьчтоделаешь. Пфф, думаю. Даже привет не буду писать. Отправил фотку плова. Сказала что тоже хочет и было бы крутым мужским поступком привезти ей горячего плова прямо с костра. А я посчитал крутым мужским поступком закинуть её везде в чс и забыть как о страшном деревенском туалете.
Материал трубопроводов зависит от назначения судовой системы и параметров прокачиваемой рабочей среды (табл. 1.1).
Трубы стальные, электросварные из углеродистой и нержавеющей стали имеют ограниченное применение в судовых трубопроводах, так как при гибке иногда появляются трещины. Биметаллические трубы, состоящие из внутреннего медного слоя толщиной 0,6 . 0,8 мм и наружного стального марок 10 и 20 и меди марки МЗр, изготавливают совместной прокаткой стальной заготовки с вставной в нее медной гильзой. Изготавливают трубы с наружным диаметром 6 . 57 мм. Широкое распространение таких труб объясняется экономией медных труб для рабочих сред с параметрами температуры до 250 °С и скорости рабочей среды до 1,2 м/с. Применяются также трубы водогазопроводные (газовые) оцинкованные или неоцинкованные (черные). Оцинкованные трубы имеют сплошное цинковое покрытие по всей наружной и внутренней поверхности.
Материалы для трубопроводов различных судовых систем
Чугунные безраструбные трубы на хомутах (типа SML фирмы «Дюкер», Германия). Хорошо зарекомендовали себя в сточных системах и системах водоснабжения. Имеют следующие свойства:
- литейный чугун с пластинчатым графитом, изготовленный методом центробежного литья;
- фитинги - литьё в форму;
- покрытие труб - снаружи эпоксидный грунт (40 мк, красно-коричневого цвета), внутри эпоксидное покрытие (120 мк, цвет жёлтый);
- прочность на разрыв: 200 МПа - для труб и 150 МПа - для фасонных частей;
- прочность на сжатие (в 3 . 4 раза больше прочности на разрыв);
- стойкость к воздействию химикатов и температур (максимальная рабочая температура 400 °С);
- высокая ударопрочность.
Как правило, их применяют в бытовых системах при давлении рабочей среды до 3 бар с хомутами «CV» и до 10 бар со специальными хомутами.
Чугунные трубы имеют следующие преимущества: полная безопасность при пожаре для людей и материального имущества, акустический комфорт, долговечность, простота сборки, минимальные затраты на обслуживание и эксплуатацию (пилятся обычной болгаркой, хомуты закручиваются обычным гаечным ключом, полная герметичность стыков). Такие трубы выпускаются с Dy 50, 70, 80, 100, 125, 150, 200, 250, 300, 400, 500, 600 мм и толщиной стенок 3 . 6 мм в зависимости от диаметра, а также к ним фитинги: крестовины, тройники, отводы с Dy 150, 300, 450, 900, заглушки (пробки), гидрозатворы, хомутные соединения. Патрубки изготавливаются переходные с одного диаметра на другой (например, с чугунных труб на пластиковые).
Трубы бесшовные из нержавеющей легированной стали. Широко применяются стали марки 08X18Н9Т с содержанием углерода до 0,08 %, хрома 18 %, никеля 9 %, титана 1 %, остальное - железо. Стандартная длина труб 1,5 . 7 м, наружный диаметр 76 мм с толщиной стенки 5 мм.
Медные трубы тянутые и прессованные. Для судовых трубопроводов применяют трубы тянутые из меди «МЗр» с наружным диаметром 3 . 360 мм и толщиной стенки 0,5 . 10 мм, длиной 1 . 6 м для рабочих сред с температурой 230 °С и скоростью 1,2 м/с. Медь не должна содержать кислорода более 0,01 % и примесей более 0,3 %. Например, бесшовные медные трубы «Frigotec» применяются для подводки технических газов в холодильных установках, кондиционерах и теплообменниках.
Медно-никелевые трубы (МНЖ5-1) содержат 5 . 6,5 % никеля, 1 . 1,4 % железа, 93 . 94 % меди. Они применяются тянутые или холоднокатаные с наружным диаметром 6 . 258 мм и толщиной стенки 1 . 4 мм, длиной 1 . 6 м (для труб забортной воды, температурой рабочих сред до 350 °С и скорости 1,2 . 3 м/с).
Трубы из сплавов цветных металлов следующих марок: «1М», «7М» и «ЗВ» с дополнительным напряжением на разрыв 190 МПа (для труб «7М», 300 МПа для труб «ЗВ»). Максимально испытываемое давление устанавливают 60 МПа. Для сплава «ЗВ» на трубе должны быть проставлены маркировка предприятия-изготовителя труб, номер партии и номер трубы, а также должен прилагаться сертификат. Эти трубы обладают высокой стойкостью против коррозии. Они применяются для трубопроводов специального назначения, имеющих повышенные требования. Диаметр труб из материалов «1М» и «7М» менее 114 мм. Трубы «ЗВ» должны выдерживать испытание на сплющивание до получения зазора, равного 90 % наружного диаметра.
Латунные трубы изготавливают тянутым или холоднокатаным способом. Чаще применяют латунные трубы марки Л62, содержащей 62 % меди и 30 % цинка; мягкие отожженные (М) и полутвердые (ПТ) после низкотемпературного отжига; кривизна на участке трубы длиной 1 м не должна превышать 5 мм.
Трубы из алюминиевого сплава применяют отожженные мягкие (м), тянутые марок «АД» и «АД1» с содержанием 98,8 % алюминия, 0,5 % железа, 0,3 % кремния, сплавов, содержащих 0,6 % марганца.
Полиэтиленовые трубы (ПЭ) обладают малым гидравлическим сопротивлением, хорошими монтажными свойствами, не отпотевают, не нуждаются в изоляции и в покрытии грунтом. Примером служит полиэтиленовая труба среднего тина с наружным диаметром 75 мм и толщиной стенки 7,1 . 8,1 мм. В трубах из полиэтилена П404-0, П2003К, П2006Т-ШО максимальный диаметр не превышает 150 мм. В зависимости от номинального условного давления напорной трубы выпускают легкие (Л) трубы, рассчитанные на давление 0,25 МПа, средние (С) на номинальное давление 0,6 МПа и тяжелые (Т) на номинальное давление 1 МПа с температурой 20 °С и не выше 49 °С.
ПЭ трубы применяют в балластных системах внутри цистерн с вязкой жидкостью; в осушительных системах для осушения небольших отсеков, для измерительных труб льял и осушительных колодцев; в качестве шпигатных труб выше палубных переборок, труб вентиляции и кондиционирования воздуха; в качестве наливных, измерительных, воздушных труб, за исключением труб в грузовых трюмах и на открытых палубах.
Трубы из материала «Полибутен-1» из ряда полиолефинов, стоящих после полиэтилена и полипропилена, выпускают следующей модификации: «Флексален-600», «Флексален-1000», «Флексален-60» диаметром от 16 до 315 мм. Имея способность выдерживать большое внутреннее давление, они отличаются высокой гибкостью и ползучестойкостью.
ПЭ трубопроводы имеют следующие преимущества:
- срок службы больше стальных труб (50 лет), а прогнозируемый срок 100 лет;
- высокая коррозионная стойкость к транспортируемым жидкостям, не требуют катодной защиты;
- незначительные затраты на обслуживание, устойчивость к большинству агрессивных сред (кислотам, щелочам, поверхностно-активным веществам, спиртам, кетонам, алифатическим углеводородам и горячим полярным растворителям, включая воду), практически не чувствительны к растрескиванию под воздействием окружающей среды;
- легче стальных труб в 2 . 4 раза, следовательно, упрощается монтаж, транспортировка и хранение;
- высокая механическая прочность;
- повышенная пропускная способность (при одинаковом диаметре на 20 . 30 % выше, чем у стальных труб);
- возможна многократная заморозка трубопровода без его разрушения (например, на газовозах и химовозах);
- высокая гибкость и надёжность соединения, что делает их незаменимыми там, где возможны вибрации и деформации корпуса и различных механизмов;
- внутренняя поверхность труб практически не зарастает и не зашлаковывается, поэтому внутреннее сопротивление труб не увеличивается со временем, в отличие от диаметра труб, который со временем увеличивается за счёт характерного для полиэтилена явления ползучести (за весь период эксплуатации примерно на 3 %);
- сборка и монтаж труб значительно надёжнее, дешевле и проще, занимают меньше времени и полностью автоматизированы (сведена к минимуму необходимость контроля качества стыков ультразвуковым методом). Благодаря простой беспламенной сварке, обеспечивается быстрая установка, лёгкость прокладки через подготовленные отверстия и выемки, использование больших пролётов труб, возможность изготовления соединительных деталей из того же материала, что и трубы (последнее значительно облегчает их установку, сокращает количество необходимых фитингов и трудозатраты по монтажу);
- экологическая безопасность для окружающей среды;
- возможность простого и надёжного присоединения к уже имеющимся системам, изготовленным из других материалов;
- устойчивость к тепловому старению;
- высокая сопротивляемость к образованию накипи и отложений;
- низкий уровень шума потока в трубах (шумы потоков воды в трубах хорошо поглощаются материалом, что создаёт более высокий уровень комфорта для потребителя по сравнения с трубами, изготовленными из металла).
Кроме того, можно пренебречь изоляцией из-за низкой теплопроводности полипропилена и избежать образования водного конденсата на внешней стороне труб (например, коэффициент теплопроводности для полипропилена λ = 0,24 Вт/(м•К); для полиэтилена λ = 0,35 Вт/(м•К); для железа λ = 50 Вт/(м•К); для меди λ = 400 Вт/(м•К)).
Система из ПЭ труб состоит из сплошных труб, которые соединяются при помощи фасонных деталей, таких как фланцевые соединения для втулок с буртиком, запорная арматура, переходные резьбовые соединения с металла на полипропилен и с полипропилена на металл, детали для присоединения арматуры и комплектующие.
Для бытовых систем применяются трубы, изготовленные из сополимерного полипропилена «PP-R100» с коэффициентом запаса прочности 1,25 для рабочих температур от 10 до 95 °С. Трубопроводы «WEFATHERM», «WEFATHERM-STAB1» снабжены алюминиевой оболочкой в основном для горячей воды. Трубы нового поколения для различных областей применения, обычно армированные волокном с более низким (на 75 %) коэффициентом линейного расширения, обозначаются «WEFATHERM-FASER».
Трубы стальные, футерованные полиэтиленом (изнутри покрыты полиэтиленом) применяют для систем забортной, пресной воды и воздуха, а также других сред, к которым полиэтилен нейтрален. Снаружи трубы покрывают антикоррозионными грунтами или смазками. Длина стандартных труб -5 м. Они условно обозначаются 16-50-ПВП с условными диаметрами от 10 до 200 мм.
Среди неметаллических труб особое место занимают металлополимерные, представляющие собой сложную многослойную конструкцию с использованием сшитого (модифицированного) полиэтилена и антидиффузионной прослойки из алюминия. Тонкая алюминиевая труба с толщиной стенки 0,5 . 2,0 мм покрыта снаружи и изнутри слоем полиэтилена (РЕХ), причём полиэтилен закреплён на поверхности алюминия клеем. Такие трубы являются надёжными, их ресурс более 50 лет. Это объясняется тем, что алюминиевая основа (сердечник) обеспечивает кислородонепроницаемость и частично компенсирует температурное расширение полиэтилена при повышенных температурах.
Слой полиэтилена предохраняет трубопроводную систему и её арматуру от образования гальванических пар с латунными и стальными элементами, придаёт гладкость внутренней поверхности и защищает её от обрастания, а кроме того, снижает коэффициент теплопроводности трубы (не более 0,45 Вт/(м •К)), что предохраняет её от запотевания, обеспечивая декоративность и чистоту наружной поверхности трубы. Металлополимерные трубы выпускаются наружным диаметром от 16 до 63 мм, свёрнутыми в бухты длиной от 200 до 50 м. Интервал рабочих температур от -40 до +95 °С. Эти трубы легко гнутся руками, режутся и стыкуются, для их соединения используются специальные фитинги (под опрессовку и зажим), что позволяет сократить трудоёмкость и продолжительность сборки. Для соединения резьбовых фитингов нужны только гаечные ключи. Недостатком данного вида труб по сравнению, например, с полимерными является чувствительность к замораживанию в заполненном водой состоянии.
Металлополимерные трубы могут применяться для различных типов систем как отдельно, так и в сочетании с другими видами труб. По сравнению с традиционными системами металлических трубопроводов данная система обеспечивает высокий уровень устойчивости к химикатам, она не подвержена воздействию коррозии и сертифицирована для транспортировки химических продуктов. Внутренняя труба «РЕХ» имеет шероховатость, в 70 раз меньшую по сравнению со стальной трубой, что обеспечивает снижение потерь давления. Следовательно, при повышенной скорости потока можно использовать меньшие размеры. Это обеспечивает экономию материалов и снижение стоимости строительно-монтажных работ.
Трубы для газовых трубопроводов из ПЭ-80 (диаметр 20 . 400 мм на рабочее давление 3 . 6 бар) и трубы из ПЭ-100 (диаметр 20 . 400 мм на рабочее давление 6 . 12 бар). Имеются ПЭ трубы повышенной надёжности с наружным защитным покрытием из специального термопласта (компания «Евротрубиласт» (Россия - Италия)), изготавливаемые из специальной марки полиэтилена повышенной плотности с двойной стенкой, гофрированные снаружи, с «двухарочной» формой гофра, и гладкие изнутри. Отличаются высокой химической стойкостью, ударопрочностью и сопротивлением стиранию.
Трубы компании «Вефатерм» (Германия) из модифицированного полипропилена PP-R100 обладают большей долговечностью и термостойкостью. Они имеют в 1000 раз меньшую шероховатость внутренней поверхности, чем металлические трубопроводы, и поэтому не являются источником дополнительного шума, возникающего в системе с высоким давлением. Выдерживают несколько циклов «замораживания-размораживания» воды. Не требуют покраски после монтажа и в процессе эксплуатации. Они в девять раз легче металлических трубопроводов, что обеспечивает соответствующую экономию при монтажных работах. Экологически практически безопасны. Такие трубы применяются в системах теплоснабжения, холодоснабжения, вентиляции, кондиционирования и др. с температурой теплоносителя до 95 °С.
В системах внутренней и наружной канализации применяют трубы из поливинилхлорида (ПВХ) - очень долговечного материала, используемого при максимальной рабочей температуре 600 °С (постоянной) и кратковременной до 950 °С. Трубы из ПВХ соединяются с помощью раструбов с запрессованными резиновыми уплотнениями и силиконовой смазкой, их максимальное давление составляет 0,5 бар. Обладают повышенной гладкостью внутри и снаружи, огнестойкостью, высокой ударопрочностью, стойкостью к воздействию химикатов, не являются канцерогеном, не поддаются коррозии, собираются быстро, легко и просто.
Отличительной особенностью изделий из ПВХ, по сравнению с другими полимерными материалами, являются трудное возгорание этого материала, его самозатухающие свойства, низкая скорость выделения тепла, что делает перспективным его применение в качестве каналов для прокладки электрических кабелей. В процессе длительной эксплуатации не происходит выделения токсичных веществ, поэтому трубы из ПВХ являются безвредными и не опасны для здоровья человека. На их внутренней поверхности не образуются бактериальные и минеральные отложения. В случае применения для водоснабжения трубопроводы из ПВХ не изменяют вкусовые качества транспортируемой воды. Диаметры труб и фитингов от 32 до 160 мм, толщина стенки 1,8, 3,2, 2,2, 4,0 мм. Например, металлопластиковые трубы из сшитого полиэтилена «РЕХ с» «РЕХ b» фирмы «Comar Multiskin» (Франция) имеют следующие преимущества:
- они в три раза легче меди, применяются для давления до 10 бар при температуре от -25 до +95 °С;
- полностью отсутствует коррозия и накипь, тепловое расширение в 10 раз меньше, чем у полиэтиленовых труб типа «РЕХ», они нечувствительны к ультрафиолетовому излучению, легко гнутся, поглощают шум, непроницаемы для кислорода, более гибки, чем любые другие типы труб, сохраняют свою форму.
Для фитингов применяется лужёная оловом латунь (в системах отопления и водоснабжения). За рубежом запрещено применение никелированных фитингов в системах водоснабжения, вызывающих аллергические реакции у потребителя. Трубы «Изопекс», применяемые в системах отопления и водоснабжения, имеют следующие параметры: рабочая температура от -100 до +95 °С, рабочее давление до 10 бар. Эти трубы эластичны, легко изгибаются, режутся и соединяются при монтаже. Они изготавливаются методом непрерывного формирования на основе применения модифицированных полиэтиленовых труб, изолированных пенополиуретаном и наружной бесшовной гидрозащитной гофрированной полиэтиленовой оболочкой. Стоимость такого трубопровода ориентировочно в 1,5 раза меньше, чем трубопровода со стальной трубой, устойчивой к химикатам и не подверженной коррозии.
Например, разработаны трубы для санитарных систем двойной экструзии (труба в трубе) от 50 мм до 150 мм из разных пластиков. Наружный слой - ПВХ с добавлением минералов, внутренний - сополимер стирола. В таком трубопроводе происходит шумопонижение, т.е. звук отражается от внутреннего слоя, а наружный слой препятствует распространению шума и вибрации материала. Отличные температурные характеристики этих труб выдерживают температуру 90 °С, коэффициент температурного расширения - 0,08 мм/(м •К).
При постройке и ремонте судов применяют различные материалы: металлы, дерево, пластмассы и др., обладающие определенными химическими, физико-механическими и технологическими свойствами, которые учитывают «при постройке и ремонте судовые конструкций.
Каждая поставляемая на судостроительный и судоремонтный заводы партия материала обязательно сопровождается документом — сертификатом, в котором указаны все его качества; в лабораториях заводов материал проходит химические, механические и технологические испытания.
При назначении марок материала для изготовления какого-либо судового изделия (деталей корпусов, механизмов, оборудования) руководствуются действующими правилами Регистра, Государственными стандартами (ГОСТ), отраслевыми нормалями (ОСТ), в которых изложены основные требования, предъявляемые к изделиям в условиях эксплуатации судов.
Сталь. Основным материалом для постройки и ремонта судов служит углеродистая сталь, а для ряда морских и смешанного плавания («река — море») судов — низколегированные стали, обладающие повышенной прочностью и облегчающие массу корпуса. При изготовлении и ремонте корпусных конструкций судов используют только стали по ГОСТ 5521—67.
Судостроительные стали в зависимости от их основных характеристик и назначения изготовляют следующих марок:
углеродистая — С, ВМСт3сн (по ГОСТ 380—71);
низколегированная — 09Г2, 09Г2С, 10Г2С1Д, 10ХСНД (по ГОСТ 5521—67).
Помимо стали ВМСт3сп, металлургические заводы поставляют стали марок: ВМСт3пс, ВМСт3кп, ВКСт3сп, ВКСт3пс, ВКСт3ки (ГОСТ 380—71).
Углеродистую сталь С применяют для постройки и ремонта морских судов; углеродистую сталь ВМСт3сп обыкновенного качества— судов внутреннего и смешанного («река — море») плавания.
Судостроительная сталь должна:
обладать некоторой устойчивостью против коррозии (в воде и на воздухе);
выдерживать обработку в горячем и холодном состояниях;
хорошо свариваться дуговой сваркой;
выдерживать загиб на 180° в холодном состоянии по оправке.
Углеродистые стали отличаются малым содержанием углерода (0,14—0,22%), серы и фосфора (не более 0,05% каждого). Сера придает металлу красноломкость, а фосфор — хладноломкость. При красноломкости металл трескается и ломается в нагретом состоянии; хладноломкость — способность металла снижать вязкость при пониженных температурах.
Низколегированные стали (вышеперечисленных марок) отличаются низким содержанием углерода (не более 0,12%); в стали добавляют легирующие элементы: кремний, марганец, хром, никель, медь.
Сталь (в соответствии с ГОСТ 5521—67) поставляют в виде листового и профильного проката; различают:
толстолистовую сталь (толщина листов 4—56 мм); тонколистовую сталь (толщина листов 0,9—3,9 мм);, фасонную (или профильную) сталь (рис. 4): равнобокий угольник, неравнобокий угольник, швеллер (корытный профиль), двутавр, углобульб, полособульб, симметричный полособульб, люковый сегментный (полукруглый), круглые профили.
В судостроении применяют и другие стали с особыми физическими или физико-механическими свойствами: ковкие стали — для изготовления мелких деталей, углеродистые и легированные — для судовых поковок, нержавеющие стали. Последние обладают высокой коррозионной устойчивостью, хорошо свариваются; из них изготовляют крылья для судов на подводных крыльях, облицовки гребных валов, лопатки турбин и др.; однако имеют повышенную стоимость, поэтому применение их ограниченное.
Алюминий. Он обладает высокой пластичностью, более высокой коррозионной стойкостью по сравнению со сплавами, созданными на его основе, но имеет низкие механические и литейные свойства, поэтому в судостроении его применяют в виде тонкой фольги, используемой в качестве теплоизоляционного материала.
Алюминиевые сплавы (в них входит 80—90% алюминия) делятся на две группы: обрабатываемые давлением и литейные.
Рис. 4. Профильный прокат:
1 — равнобокий угольник, 2 — неравнобокий угольник, 3 — швеллер, 4 — двутавр, 5 — углобульб, 6 — полособульб, 7 — симметричный полособульб, 8 — люковый профиль, 9— сегментный профиль, 10 — прутковая сталь
Алюминиевые сплавы, обрабатываемые давлением (деформируемые). Рассматриваемые сплавы бывают термически неупрочняемые и упрочняемые.
Термически неупрочняемые сплавы (по сравнению с упрочняемыми) обладают меньшей прочностью, но гораздо более высокой антикоррозионной стойкостью, повышенной пластичностью, хорошей свариваемостью.
К термическим неупрочняемым сплавам относятся: алюминиево-марганцевый и алюминиево-магниевый сплавы.
Алюминиево-марганцевый сплав АМц обладает низкой прочностью, имеет высокую антикоррозионную стойкость и большую пластичность в отожженном состоянии; хорошо сваривается; применяют для изготовления легких выгородок, баков для жидкостей (кроме щелочей и кислот), вентиляционных труб и др.
Алюминиево-магниевые сплавы АМг, АМг5, АМг5В, АМгб, АМг61 обладают высокими антикоррозионными свойствами; при содержании магния меньше 3% прочность их незначительна, при большем содержании магния (свыше 5,5%) прочность сплава увеличивается, но понижается сопротивление коррозии.
Сплавы АМг и АМг5 применяют для изготовления малонагруженных конструкций: легких переборок, трубопроводов, арматуры, бачков, а также для внутренней отделки судов; хорошо свариваются контактной и аргонно-дуговой сваркой, несколько хуже газовой. Из сплава АМг5 изготовляют заклепки.
Сплав АМг5В (средней прочности) наиболее коррозионноустойчив. Сплавы АМг5В, АМгб, АМг61 применяют для изготовления нагруженных прочностных конструкций корпусов судов; хорошо свариваются контактной и аргонно-дуговой сваркой.
К термически упрочняемым сплавам относятся алюминиево-медные сплавы и алюминиевые сплавы для ковки и штамповки.
Алюминиево-медные сплавы (дуралюмины) до изготовления корпусов судов обрабатывают, а затем закаляют в особых масляных ваннах с быстрым охлаждением; имеют прочность, равную прочности некоторых малоуглеродистых сталей. В состав дуралюминов, кроме меди, магния и кремния, упрочняющих сплавы, входит марганец, способствующий измельчению структуры металла. Серьезным недостатком этих сплавов является низкая их антикоррозионная стойкость.
Дуралюмин Д1 применяют для изготовления малонагруженных конструкций корпуса: настилов в корпусе, внутренней обшивки, трапов, дверей, стоек, судовой мебели, а сплав Д6 — для изготовления нагруженных конструкций: переборок, кронштейнов, раскосов. Из сплава Д16, обладающего высокой прочностью, изготовляют заклепки, обшивку и набор корпусов и конструкций.
Алюминиевые сплавы для ковки и штамповки в качестве основы имеют алюминиево-медные сплавы с добавкой легирующих элементов: магния, никеля, железа и кремния. В судостроении применяют сплав АК4, обладающий относительно высокой прочностью, используемый для изготовления несложных штамповок и поковок.
Алюминиевые литейные сплавы сохраняют свойства чистого алюминия с присадками (кремний, магний, медь и цинк), которые улучшают литейные свойства сплава, повышают прочность и твердость, но одновременно уменьшают его пластичность, антикоррозионную стойкость, тепло- и электропроводность.
Алюминиево-кремниевые сплавы (силумины) применяют при фасонном литье. Из сплава АЛ2 изготовляют арматуру, коробки, маховики, барашки, кронштейны и др.
Алюминиево-магниевые сплавы обладают по сравнению с силуминами более высокой антикоррозионной стойкостью и лучшими механическими свойствами.
Наибольшее применение получили сплавы АЛ8 (в закаленном состоянии), АЛ 13 и 45Мг2; из АЛ8 и АЛ 13 изготовляют детали арматуры масляных и топливных систем, вентиляции и дельных вещей; из сплава 45Мг2 —детали и изделия (трубопроводы пресной воды, масляные и топливные системы, судовые механизмы и оборудование, дельные вещи), работающие при высокой температуре, но не выше 100° С.
Основным преимуществом всех алюминиевых сплавов является их малая плотность (2,6—2,8 г/см 3 ), что в три раза меньше плотности судостроительной стали (7,85 г/см 3 ). Поэтому алюминиевые сплавы широко применяют для постройки судов облегченного типа (СПК, СВП, полуглиссеров), а также для изготовления надстроек крупных пассажирских судов.
Лесоматериалы. Все древесные породы делят на хвойные и лиственные. Из хвойных пород в судостроении применяют: сосну, ель, лиственницу, пихту и кедр. Из лиственных — березу, дуб, ясень и красное дерево.
Лесоматериалы применяют в виде бревен, брусьев, брусков, досок, фанеры, столярных и древеснослоистых плит.
Бревна и брусья используют для изготовления деталей, поддерживающих корпусные конструкции при сборке на стапеле и на сборочных площадках.
Из брусков изготовляют обрешетники, подножные решетки и другие судовые конструкции; из досок — переборки, настилы и др.
Фанеру используют для изоляции и декоративной отделки помещений; выпускают различных марок и типоразмеров толщиной от 0,8 до 16 мм; изготовляют из шпона (тонкий слой древесины толщиной 0,4—0,7 мм) различных пород дерева — березы, ореха, дуба и др.
Столярные плиты — это клееные щиты, основа (внутренняя часть) которых состоит из брусков дерева хвойных пород, соединенных между собой клеем или вшпунт, а рубашки (наружная часть) — из шпона или фанеры, наклеенных на основу. Из плит изготовляют крышки столов, боковые стенки и полки шкафов, панели и переборки судовых помещений.
Древеснослоистыё пластики (ДСП) изготовляют в виде плит из листов березового шпона, пропитанных фенолформальдегидными смолами и клеенных при высокой температуре (до 150° С) под давлением (до 300 кГс/см 2 ).
Для защиты древесины от загнивания и придания ей огнестойкости ее пропитывают специальными растворами — антисептиками и антипиренами.
В судостроении применяют материалы, получаемые на химических заводах при помощи синтеза различных органических веществ. В основном используют эластики и пластики (пластмассы).
Эластики обладают высокой эластичностью и сохраняют свою первоначальную форму после снятия усилий.
Пластмассы применяют для изготовления крупногабаритных конструкций, устанавливаемых на металлических корпусах: надстроек, рубок, капов и др., а также переборок и выгородок внутри корпуса. Применение синтетических материалов для изготовления судовых конструкций стало возможным в результате создания специальной группы пластмассовых материалов — стеклопластиков. Этот материал по сравнению с металлом и деревом обладает большой относительной прочностью, не магнитен, не корродирует, стоек против гниения, красится в процессе полимеризации и др.
Стеклопластик — материал сложной композиции, основными составляющими которого является связующее (смола с различными добавками), и армирующий материал. В качестве связующего для стеклопластиков используют ненасыщенные полиэфирные смолы холодного отверждения; армирующий материал — стекловолокнистые наполнители: стеклохолсты, стекложгут, стеклоткани разнообразного плетения. Тканевые материалы подразделяют на ткани из крученых и некрученых нитей (жгутовые ткани или стеклорогожки).
Плотность стеклопластиков зависит от материала и объема армирования и составляет 1,6—1,8 г/см 3 ; стеклопластики в 5 раз легче стали и в среднем примерно в 2 раза легче алюминиевых сплавов.
Чем больше в пластике содержится стекловолокна, тем он прочнее; содержание стекловолокна по массе; изменяется от 30 до 60%, а иногда до 70%, что соответствует 15—40% по объему. Разместить в пластике большее количество стекловолокна и тем самым повысить прочность материала не удается, так как при этом смола не будет надежно закрывать со всех сторон наполнитель.
Стеклопластик подвержен старению, и «прочностные показатели его снижаются как при продолжительном действии нагрузки, так и без нее. Снижение предела прочности только в результате старения составляет 10—20% за 10 лет.
При погружении стеклопластиков в морскую или речную воду прочность его снижается (особенно в первые 10 суток) примерно на 25—35%, а затем незначительно. Для уменьшения величины снижения предела прочности стеклопластика армирующий материал (стеклоткань) обрабатывают гидрофобноадгезионными составами, отталкивающими воду. Например, состав ГВС-9 снижает потери прочности до 10—12%, зависящие от марки смолы и стекловолокнистых наполнителей.
Стеклохолст — армирующий материал, обеспечивает наиболее равномерные (одинаковые по всем направлениям) прочностные свойства стеклопластика. Химически связанный стеклохолст представляет собой хаотически расположенное рубленое волокно, соединенное специальными эмульсиями; легко пропитывается смолой; значительно дешевле стеклотканей. Прочность стеклопластиков, полученных на основе стеклохолста, относительно невелика, поэтому их применяют для изготовления малонагруженных судовых конструкций (надстроек, выгородок и др.) и корпусов мелких судов (катеров, лодок).
Стекложгут используют для подкрепления конструкций в строго определенном направлении (например, для армирования свободных поясков балок набора); применяют для производства балок таврового или полособульбового профиля способом непрерывной протяжки на специальных машинах. В таких балках жгуты во всех элементах ориентированы параллельно направлению подкрепления. Стекложгут применяют также для получения рубленого волокна при изготовлении стеклопластика методом напыления; этот материал (рубленое волокно) близок по свойствам к стеклопластику, армированному стеклохолстом.
Стеклоткани сатинового переплетения и кордные ткани, используемые в качестве армирующего материала, обеспечивают относительно высокую прочность стеклопластика.
У тканей сатинового переплетения каждая нить основы (нити, идущие вдоль направления рулона) проходит над определенным количеством нитей утка, а затем — над группой таких нитей. В этих тканях нет крупных перегибов нитей, как в тканях полотняного переплетения. Поэтому стеклопластики на их основе обладают большей прочностью и жесткостью; эластичны, хорошо укладываются по обводам формы и легко пропитываются смолой. Эти свойства обусловили их широкое применение в судостроении.
Кордные ткани изготовляют как из крученых, так и некрученых нитей. Нити основы кордных тканей связаны относительно слабыми нитями утка и не имеют перегибов. Стеклопластик, армированный кордными тканями, применяют для усиления связей в определенном направлении (например, для палубного стрингера, ширстрека, горизонтального киля, поясков балок и др.).
Изоляционные материалы применяют на судах для тепловой, противопожарной и противошумной изоляции; не должны поддерживать горения, быть стойкими к воздействию влаги, для чего изоляцию покрывают сверху шпаклевкой и окрашивают.
Покрасочные материалы служат для покрытий всех судовых поверхностей. К ним относятся: масляные, смоляные и силикатные краски, свинцовый и железный сурик, белила, лаки, синтетические краски, эмали (на основе пентафталевых смол), этинолевые краски, кузбасский лак и др.
Для лучшей защиты судовых конструкций и обеспечения более длительного срока их службы лакокрасочные покрытия наносят на тщательно зачищенные и загрунтованные поверхности.
Подводные поверхности корпусов морских судов покрывают специальными красками, более стойкими против обрастания корпуса ракушками и водорослями.
Клеи применяются для соединения различных деталей судового оборудования и корпусных конструкций; должны обладать хорошей адгезией (способностью прилипать к поверхности), достаточной прочностью, огнестойкостью, температуроустойчивостью, нетоксичностью и технологичностью.
Бетон получают смешивая судостроительный цемент с водой и наполнителями (песок, щебень и гравий) в определенных пропорциях. Конструктивное соединение бетона и стальной арматуры — железобетон отличается не только хорошей твердостью, но и способностью частично работать на растяжение; применяют для изготовления корпусов железобетонных судов, покрытия палуб, ремонта отдельных корпусных конструкций стальных судов.
Мастики применяют для защиты палуб от воздействия влаги и придания им большей стойкости против механических воздействий и искрообразования (на танкерах). В судостроении и судоремонте применяют специальные мастики (типа «Нева» и др.); ими покрывают палубы после окончания сварочных работ и испытаний их на водонепроницаемость.
К прочим неметаллическим судостроительным материалам относятся: резина, применяемая для прокладок, уплотнения горловин, иллюминаторов, люков, дверей и др.; кожа — для различных прокладок, манжет и отделки мебели (широко используется искусственная кожа); стекло — для изготовления иллюминаторов, зеркал, водоуказательных стекол и др. В качестве отделочных материалов находят применение линкруст, повинол, различные ткани и др.
Корпус судна на подводных крыльях (СПК) имеет характерную особенность конструкций в подводной части в виде крыльев, расположенных в носу и корме. При движении с малой скоростью судно передвигается как обычное, а с увеличением скорости крылья приобретают подъемную силу и корпус судна полностью выходит из воды (рис. 7.17). Следовательно, корпус такого судна может длительное время находиться в морской воде, что приводит к его обрастанию. На ходу он подвергается действию потока и брызг воды, воздуха и солнца, что способствует возникновению и быстрому развитию коррозионных процессов. Кроме того, в результате взаимодействия крыльевых устройств и корпуса судна, происходят интенсивные коррозионные разрушения корпуса изготовляемого обычно из легких сплавов.
Рис. 7.17. Схема судна на подводных крыльях. 1 — кормовая палуба; 2 — кормовой салон; 3 — служебные помещения; 4 — машинное отделение; 5 — коридор; 6 — съемный тент; 7 — средний салон; 8 — водонепроницаемые объемы; 9 — входной тамбур; 10 — ходовая рубка; 11 — носовой салон; 12 — форпик.
Для защиты корпуса от коррозии и обрастания необходимо: использовать покрытия, не разрушающиеся при электрохимической защите; применять схемы окрашивания, обеспечивающие защиту от коррозии, особенно в местах контакта конструкций из разнородных металлов, на срок не менее одного года; наносить противообрастающие покрытия, обеспечивающие защиту крыльевых устройств и подводной части корпуса от обрастания; применять для крыльев и подводной части корпуса твердые, износостойкие покрытия, обладающие высокой адгезией, не поддающиеся разрушению или только в очень малой степени разрушающиеся в районе входной кромки крыла. При окрашивании крыльевых устройств должны применяться покрытия с максимальной кавитационной стойкостью. К таким покрытиям относятся эпоксидные и полиурстановые, горячей сушки и эпоксидно-каменноугольные холодной и горячей сушки.
Крыльевые устройства на рассматриваемых судах окрашивают только тремя-четырьмя слоями противокоррозионной краски, так как после одного-двух подъемов из воды некоторые типы противообрастающих красок приходится полностью возобновлять. Для повышения адгезии наносимых красок крыльевые устройства делают шероховатыми (обрабатывая их песком или очень мелкой дробью). С помощью краскораспылителя краску наносят обязательно поперек крыла. Покрытие должно иметь минимальную шероховатость, что обеспечивается применением красок с хорошим розливом или шлифованием нанесенной краски для устранения неровностей покрытия.
При эксплуатации катодный осадок удаляют шлифованием и последующим окрашиванием мест с нарушенным покрытием. Осевшие личинки морских организмов, пока они не закрепились и не вросли в краску, удаляют, протирая крылья старыми капроновыми сетями.
Суда на воздушной подушке (СВП) (рис. 7.18) могут двигаться на мелководье, по болотистым местам, песку, снегу и т. д. Во время движения под днище специальными вентиляторами непрерывно нагнетается воздух, что позволяет судну парить над поверхностью. При этом днище и нижняя часть корпуса находятся в необычайно жестких условиях. Поступающий в нагнетательную камеру воздух захватывает песок, поднимает с земли мелкие камни и другие предметы, которые с силой ударяются о днище, разрушая на нем защитные покрытия. Поэтому при окрашивании СВП основное внимание должно быть уделено защите нижней части корпуса и днища. Применяемые краски должны обладать: высокой абразивной стойкостью и хорошей адгезией: отличными противокоррозионными свойствами; быть устойчивыми при длительном действии на них воды, водяных брызг и атмосферных осадков. Такими красками могут быть эпоксидные, полиуретановые, эпоксидно-каменноугольные (ЭП-72, «Инерта-160»), типа ЭФ-1144 и др.
Рис. 7.18. Судно на воздушной подушке.
1 — вентилятор; 2 — воздушная шахта; 3 — воздушный канал; 4 — ватерлиния при неработающем вентиляторе; 5 — ватерлиния при работающем вентиляторе; 6 — нагнетаемый воздух; 7 — отсек плавучести.
Более надежную защиту днища от абразивного износа обеспечивает невысыхающая вязкая мастика (№ 579, 580 и др.), состоящая из битума, асбестового волокна, минеральных масел, специальных смол. Наносят ее краскораспылителем или шпателем.
В подводной части сильный износ покрытий наблюдается в верхней части нагнетательной шахты, куда поступает воздух, загрязненной абразивом. Воздух, засасываемый в шахту, по пути попадает на лобовую часть судна, разрушая на нем покрытие. Эти участки при постройке следует окрашивать дополнительным слоем краски, а в процессе эксплуатации систематически осматривать и окрашивать.
Автор статьи
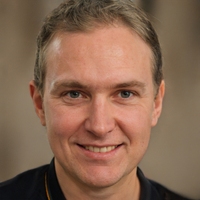
Читайте также:
- Можно ли проводить орм проверочная закупка без санкции суда
- Можно ли отдать квартиру государству в счет погашения долга по жкх
- Невозможно попасть к судебному приставу что делать
- Судебная практика по гражданским делам о взыскании денежных средств по договору купли продажи
- Не вниди в суд с рабом твоим что значит